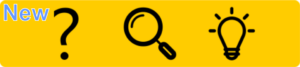
Fault Code + Description | Code + Subcode | Fault Name | Fault Type | Description | Cause | Remedy (Troubleshooting) | Note |
---|---|---|---|---|---|---|---|
Fault 1 : Notice: it is recommended to perform a power reboot of the system | 1.9 | Reboot reminder | Info | Notice: it is recommended to perform a power reboot of the system | 9 months since last power reset of the system | Reset the power supply within 3 months | Lift remains in operation. The reset timer is indipendent from system data/time settings |
Fault 1 : A power reboot of the system is required | 1.12 | Reboot reminder | Alert | A power reboot of the system is required | 12+ months since last power reset of the system. The lift is out of service | Reset the power supply | The reset timer is indipendent from system data/time settings |
Fault 1 : The automatic return to floor emergency maneuver is completed: the car is at floor with the doors open. The system can return to operation as soon as power is restored. | 1.100 | Emergency manouver completed | Info | The automatic return to floor emergency maneuver is completed: the car is at floor with the doors open. The system can return to operation as soon as power is restored. | No action required | This alert appears only in case of emergency operation. After power reset, the fault is overwritten by Subcode 101 | |
Fault 1 : The system is powered again | 1.101 | System restart | Info | The system is powered again | No action required | Repeated reset reports may indicate a power problem, electromagnetic interference, or motherboard defect | |
Fault 1 : The system is powered again | 1.102 | System restart | Info | The system is powered again | No action required | Repeated reset reports may indicate a power problem, electromagnetic interference, or motherboard defect | |
Fault 1 : A remote reset of the errors in memory was carried out via the Fusion app (Note: errors with special/specific reset are excluded) | 1.255 | Remote Reset | Info | A remote reset of the errors in memory was carried out via the Fusion app (Note: errors with special/specific reset are excluded) | No action required | ||
Fault 2 : One or more of the NC contacts associated with the contactors (“CCO” input) remained open after the cabin stopped at floor. | 2.0 | Contactors blocked | Alert | One or more of the NC contacts associated with the contactors (“CCO” input) remained open after the cabin stopped at floor. | Loose contact on CCO circuit or broken contactor. | Check: 1) The series of auxiliary contacts (NC) of the contactors and the other cables in series in the CCO circuit 2) The wiring of the CCO circuit wiring as indicated in the wiring schematics 3) The CCO input of the Mother board (connectors J22 or J23 or J14) | CCO input status can be monitored in the “I/O status” menu of the PlayPad, (Playboard in/out submenu, page 2) |
Fault 2 : One or more of the NC contacts associated with the contactors (input CCOB) remained open after the car stopped at floor. | 2.1 | Contactors blocked | Alert | One or more of the NC contacts associated with the contactors (input CCOB) remained open after the car stopped at floor. | Loose contact on CCOB circuit or broken contactors | Check: 1) The series of auxiliary contacts (NC) of contactors and the other cables in series in the CCOB circuit 2) The wiring of the CCOB circuit wiring as indicated in the wiring schematics 3) The CCOB input of the Mother board (VVVF controller: connectors J22 or J23 or J14) | CCOB input is viewable via Playpad in I/O status menu, Playboard in/out page 2 |
Fault 2 : One or more of the NC contacts associated with the contactors and wired in series to the “CCO+CCOB” inputs, remained open after the car stopped at floor. | 2.2 | Contactors blocked | Alert | One or more of the NC contacts associated with the contactors and wired in series to the “CCO+CCOB” inputs, remained open after the car stopped at floor. | Loose contact on CCO circuit or broken motor contactor. Loose contact on CCOB circuit or broken contactors. | Check: 1) The series of auxiliary contacts (NC) of the contactors and the other cables in series in the CCO circuit 2) The wiring of the CCO circuit wiring as indicated in the wiring schematics 3) The CCO input of the Mother board (connectors J22 or J23 or J14) 4) The series of auxiliary contacts (NC) of contactors and the other cables in series in the CCOB circuit 5) The wiring of the CCOB circuit wiring as indicated in the wiring schematics 6) The CCOB input of the Mother board (VVVF controller: connectors J22 or J23 or J14) | CCO and CCOB inputs are viewable via Playpad in I/O status menu, Playboard in/out page 2 |
Fault 2 : The NC contact associated with the MOTOR power contactor CM1 remained open after the car stopped at floor. | 2.11 | Contactors blocked | Alert | The NC contact associated with the MOTOR power contactor CM1 remained open after the car stopped at floor. | Loose contact on YBRK circuit or broken motor contactor CM1 (Only for Direct or Hydro+VVF Option) | Check: 1) The auxiliary contact (NC) of the motor contactor 2) The wiring of the YBRK circuit wiring as indicated in the wiring schematics 3) The YBRK input of the Mother board connector J23 | YBRK input is viewable via Playpad in I/O status menu, Playboard in/out page 2 |
Fault 2 : The NC contact associated with the MOTOR power contactor CM2 remained open after the car stopped at floor. | 2.12 | Contactors blocked | Alert | The NC contact associated with the MOTOR power contactor CM2 remained open after the car stopped at floor. | Loose contact on CCO circuit or broken motor contactor CM2 (Only for Direct or Hydro+VVF Option) | Check: 1) The auxiliary contact (NC) of the motor contactor 2) The wiring of the CCO circuit wiring as indicated in the wiring schematics 3) The CCO input of COIL board (connectors J2 or JM1) or on the Mother board connector J22 | CCO input is viewable via Playpad in I/O status menu, Playboard in/out page 2 |
Fault 2 : One of the NC contacts associated with the MOTOR power contactors CM1 or CM2 remained open after the car stopped at floor. | 2.13 | Contactors blocked | Alert | One of the NC contacts associated with the MOTOR power contactors CM1 or CM2 remained open after the car stopped at floor. | Loose contact on CCO circuit or broken motor contactors CM1 or CM2 (Only for Soft Starter Option) | Check: 1) The auxiliary contacts (NC) of the motor contactors 2) The wiring of the CCO circuit wiring as indicated in the wiring schematics 3) The CCO input of COIL board (connectors J2 or JM1) or on the Mother board connector J22 | CCO input is viewable via Playpad in I/O status menu, Playboard in/out page 2 |
Fault 2 : The contact associated with the Soft Starter remained open after the controller try to start the motor | 2.14 | Contactors blocked | Alert | The contact associated with the Soft Starter remained open after the controller try to start the motor | Loose contact on YBRK circuit or Soft Starter END output Only for Soft Starter Option) | Check: 1) The auxiliary contact (NO) of the motor contactor CM2 2) The RUN input of Soft Starter or M2 connector on COIL board 3) The END Output of Soft Starter 4) The wiring of the YBRK circuit wiring as indicated in the wiring schematics 5) The YBRK input of the Mother board connector J23 | YBRK input is viewable via Playpad in I/O status menu, Playboard in/out page 2 |
Fault 2 : One of the NC contacts associated with the MOTOR power contactors CM2 or CM3 remained open after the car stopped at floor. | 2.15 | Contactors blocked | Alert | One of the NC contacts associated with the MOTOR power contactors CM2 or CM3 remained open after the car stopped at floor. | Loose contact on CCO circuit or broken motor contactors CM2 or CM3 (Only for Star Delta Option) | Check: 1) The series of auxiliary contacts (NC) of the motor contactors CM2 and CM3 and the other cables in series in the CCO circuit 2) The wiring of the CCO circuit wiring as indicated in the wiring schematics 3)The CCO input of COIL board (connectors J2 or JM1) or on the Mother board connector J22 | CCO input is viewable via Playpad in I/O status menu, Playboard in/out page 2 |
Fault 2 : One of the NC contacts associated with the VALVE’s contactors remained open after the car stopped at floor. | 2.200 | Contactors blocked | Alert | One of the NC contacts associated with the VALVE’s contactors remained open after the car stopped at floor. | Loose contact on CCOB circuit or broken VALVE’s contactors. | Check: 1) The series of auxiliary contacts (NC) of the VALVE contactors and the other cables in series in the CCOB circuit 2) The wiring of the CCOB circuit wiring as indicated in the wiring schematics 3) The CCOB input of COIL board (connectors J2 or JV3) or on the Mother board connector J14 | CCOB input is viewable via Playpad in I/O status menu, Playboard in/out page 2 |
Fault 3 : Lift moved at low speed for too long (the fault appears if the lift does not reach the floor once it has received the low speed command from the controller within the set time). | 3.1 | Low speed too long | Warning | Lift moved at low speed for too long (the fault appears if the lift does not reach the floor once it has received the low speed command from the controller within the set time). | The error appears if the lift does not reach the floor within the set time (modifiable parameter) after receiving the low-speed command from the controller. The cause could be the low torque of the motor when approaching the floor or a non-optimal adjustment of the inverter parameters when approaching the floor. | Check: 1) The parameter related to the fault timing (https://dido.dmg.it/it/knowledge-base/controller-p40/#configuration-menu); increase it if necessary 2) The speed of the lift when in “low speed” mode. Increase it if necessary. Increase parameter C07 in steps of 2 Hz (Playpad, VVVF advanced menu, https://dido.dmg.it/knowledge-base/controller-p40/#vvvf-menu) 3) Increase the value of P06 (PlayPad, VVVF Advanced menu, https://dido.dmg.it/knowledge-base/controller-p40/#vvvf-menu) up to a maximum of 60% of P03 (nominal value) 4) The slowdown distance to the indicated floor, or increase the E13 deceleration ramp (PlayPad, VVVF Advanced menu, https://dido.dmg.it/knowledge-base/controller-p40/#vvvf-menu). | |
Fault 3 : Lift moved at low speed for too long (the fault appears if the lift does not reach the floor once it has received the low speed command from the controller within the set time). | 3.2 | Low speed too long | Warning | Lift moved at low speed for too long (the fault appears if the lift does not reach the floor once it has received the low speed command from the controller within the set time). | The error appears if the lift does not reach the floor within the set time (modifiable parameter) after receiving the low-speed command from the controller. The cause could be the low torque of the motor when approaching the floor or a non-optimal adjustment of the inverter parameters when approaching the floor. | Check: 1) The parameter related to the fault timing (https://dido.dmg.it/it/knowledge-base/controller-p40/#configuration-menu); increase it if necessary 2) The speed of the lift when in “low speed” mode. Increase it if necessary. Increase the stopping boost in steps of 2% (PlayPad, System Positioning menu, https://dido.dmg.it/knowledge-base/controller-p40/#system-positioning-menu) 3) Increase the value of P06 (Playpad, VVVF menu advanced, https://dido.dmg.it/knowledge-base/controller-p40/#vvvf-menu, no-load current) up to a maximum of 60% of P03 (nominal value); 4) the R1D/R1S distance value (Playpad, System Positionig menu, https://dido.dmg.it/it/knowledge-base/controller-p40/#system-positioning-menu). | |
Fault 3 : Lift moved at low speed for too long (the fault appears if the lift does not reach the floor once it has received the low speed command from the controller within the set time). | 3.3 | Low speed too long | Warning | Lift moved at low speed for too long (the fault appears if the lift does not reach the floor once it has received the low speed command from the controller within the set time). | The error appears if the lift does not reach the floor within the set time (modifiable parameter) after receiving the low-speed command from the controller. The cause could be the low torque of the motor when approaching the floor or a non-optimal adjustment of the inverter parameters when approaching the floor. | Check: 1) The parameter related to the fault timing (https://dido.dmg.it/it/knowledge-base/controller-p40/#configuration-menu); increase it if necessary 2) The speed of the lift when in “low speed” mode. Increase it if necessary. Increase the stopping boost in steps of 2% (PlayPad, System Positioning menu, https://dido.dmg.it/knowledge-base/controller-p40/#system-positioning-menu) 3) Increase the value of P06 (Playpad, VVVF menu advanced, https://dido.dmg.it/knowledge-base/controller-p40/#vvvf-menu, no-load current) up to a maximum of 60% of P03 (nominal value); 4) the R1D/R1S distance value (Playpad, System Positionig menu, https://dido.dmg.it/it/knowledge-base/controller-p40/#system-positioning-menu). | |
Fault 3 : Lift moved at low speed for too long (the fault appears if the lift does not reach the floor once it has received the low speed command from the controller within the set time). | 3.4 | Low speed too long | Warning | Lift moved at low speed for too long (the fault appears if the lift does not reach the floor once it has received the low speed command from the controller within the set time). | The error appears if the lift does not reach the floor within the set time (modifiable parameter) after receiving the low-speed command from the controller. The cause could be the low torque of the motor when approaching the floor or a non-optimal adjustment of the inverter parameters when approaching the floor. | Check: 1) The parameter relating to the error timing (https://dido.dmg.it/it/knowledge-base/controller-p40/#configuration-menu); increase it if necessary 2) The speed of the elevator at low speed. Increase it if necessary. Increase the stopping boost in steps of 2% (PlayPad, System Positioning menu, https://dido.dmg.it/knowledge-base/controller-p40/#system-positioning-menu) 3) Increase the value of P06 (Playpad, VVVF menu advanced, https://dido.dmg.it/knowledge-base/controller-p40/#vvvf-menu, no-load current) up to a maximum of 60% of P03 (nominal value); 4) the R1D/R1S distance value (Playpad, System Positionig menu, https://dido.dmg.it/it/knowledge-base/controller-p40/#system-positioning-menu). | |
Fault 3 : Lift moved at low speed for too long (the fault appears if the lift does not reach the floor once it has received the low speed command from the controller within the set time). | 3.5 | Low speed too long | Warning | Lift moved at low speed for too long (the fault appears if the lift does not reach the floor once it has received the low speed command from the controller within the set time). | The error appears if the lift does not reach the floor within the set time (modifiable parameter) after receiving the low speed command from the panel. The cause could be the low temperature of the oil in the pump. | Check: 1) The parameter relating to the fault timing (https://dido.dmg.it/it/knowledge-base/controller-p40/#configuration-menu); increase it if necessary 2) The slowdown distance to the indicated floor (FAI/FAS magnets) 3) The valve activation circuit (see electrical diagram) | |
Fault 3 : Lift moved at low speed for too long (the fault appears if the lift does not reach the floor once it has received the low speed command from the controller within the set time). | 3.6 | Low speed too long | Warning | Lift moved at low speed for too long (the fault appears if the lift does not reach the floor once it has received the low speed command from the controller within the set time). | The error appears if the lift does not reach the floor within the set time (modifiable parameter) after receiving the low speed command from the panel. The cause could be the low temperature of the oil in the pump. | Check: 1) The parameter related to the fault timing (https://dido.dmg.it/it/knowledge-base/controller-p40/#configuration-menu); increase it if necessary 2) the R1D/R1S distance value (Playpad System Positioning menu, https://dido.dmg.it/it/knowledge-base/controller-p40/#system-positioning-menu) 4) Valve activation circuit (see diagram electric) 3) The valve activation circuit (see electrical diagram) | |
Fault 3 : Lift moved at low speed for too long (the fault appears if the lift does not reach the floor once it has received the low speed command from the controller within the set time). | 3.7 | Low speed too long | Warning | Lift moved at low speed for too long (the fault appears if the lift does not reach the floor once it has received the low speed command from the controller within the set time). | The error appears if the lift does not reach the floor within the set time (modifiable parameter) after receiving the low speed command from the panel. The cause could be the low temperature of the oil in the pump. | Check: 1) The parameter related to the fault timing (https://dido.dmg.it/it/knowledge-base/controller-p40/#configuration-menu); increase it if necessary 2) the R1D/R1S distance value (Playpad System Positioning menu, https://dido.dmg.it/it/knowledge-base/controller-p40/#system-positioning-menu) 4) Valve activation circuit (see diagram electric) 3) The valve activation circuit (see electrical diagram) | |
Fault 3 : Lift moved at low speed for too long (the fault appears if the lift does not reach the floor once it has received the low speed command from the controller within the set time). | 3.0 | Low speed too long | Warning | Lift moved at low speed for too long (the fault appears if the lift does not reach the floor once it has received the low speed command from the controller within the set time). | The error appears if the lift does not reach the floor within the set time (modifiable parameter) after receiving the low speed command from the panel. The cause could be: – For Electric Controller, the low torque of the motor when approaching the floor or a non-optimal adjustment of the inverter parameters when approaching the floor. – For Hydraulic Controller, the low temperature of the oil in the pump. | For Electric Controller, check: 1) The parameter related to the fault timing (https://dido.dmg.it/it/knowledge-base/controller-p40/#configuration-menu); increase it if necessary 2) The speed of the lift when in “low speed” mode. Increase it if necessary. Increase parameter C07 in steps of 2 Hz (Playpad, VVVF advanced menu, https://dido.dmg.it/knowledge-base/controller-p40/#vvvf-menu) in case of magnet and magnetic switch. Increase the stopping boost in steps of 2% (PlayPad, System Positioning menu, https://dido.dmg.it/knowledge-base/controller-p40/#system-positioning-menu) in case of DMG Rope Encoder or ELGO or Motor Encoder 3) Increase the value of P06 (PlayPad, VVVF Advanced menu, https://dido.dmg.it/knowledge-base/controller-p40/#vvvf-menu) up to a maximum of 60% of P03 (nominal value) 4) The slowdown distance to the indicated floor, or increase the E13 deceleration ramp (PlayPad, VVVF Advanced menu, https://dido.dmg.it/knowledge-base/controller-p40/#vvvf-menu) in case of magnet and magnetic switch. The R1D/R1S distance value (Playpad, System Positionig menu, https://dido.dmg.it/it/knowledge-base/controller-p40/#system-positioning-menu) in the other cases. For Hydraulic controller, check 1) The error timing parameter (https://dido.dmg.it/it/knowledge-base/controller-p40/#configuration-menu); increase it if necessary 2) the distance value R1D/R1S in the case of a counting system via DMG encoder or via ELGO (Playpad counting menu, https://dido.dmg.it/it/knowledge-base/controller-p40/#system-positioning-menu). The deceleration distance to the indicated floor (FAI/FAS magnetic readers) 3) The valve activation circuit (see circuit diagram). | |
Fault 4 : Car overload. The lift does not start. | 4.0 | Overload | Alert | Car overload. The lift does not start. | Excessive load in the lift cabin. Overload input SUR is activated | Check: 1) The SUR input (if locked) and wiring; 2) The setting of the load weighing device (https://dido.dmg.it/knowledge-base/llec6-load-weighing-device/) | SUR input is viewable via Playpad in I/O status menu, Playboard in/out page 1 |
Fault 5 : A discrepancy between the calculated position of the car and the actual one was detected | 5.1 | Positioning fault | Warning | A discrepancy between the calculated position of the car and the actual one was detected | A difference between the calculated position of the car and the real one was detected in correspondence of the activation of one of the AGB/AGH limit switches. | Check: 1) The correct positioning of the magnets 2) The operation of the magnetic pulsers 3) The distance between extreme contact and magnet | |
Fault 5 : A discrepancy between the calculated position of the car and the actual one was detected | 5.2 | Positioning fault | Warning | A discrepancy between the calculated position of the car and the actual one was detected | A difference between the calculated position of the car and the real one was detected in correspondence of the activation of one of the AGB/AGH limit switches. | Check: 1) The correct positioning of the magnets 2) The operation of the magnetic pulsers 3) The distance between extreme contact and magnet 4) The correct operation/connection of the encoder | The tolerance is up to 5 cm compared to the learning quota. |
Fault 5 : A discrepancy between the calculated position of the car and the actual one was detected | 5.3 | Positioning fault | Warning | A discrepancy between the calculated position of the car and the actual one was detected | A difference between the calculated position of the car and the real one was detected in correspondence of the activation of one of the AGB/AGH limit switches. | Check: 1) The correct positioning of the magnets 2) The operation of the magnetic pulsers 3) The distance between extreme contact and magnet 4) The correct operation/connection of the encoder | The tolerance is up to 5 cm compared to the learning quota. |
Fault 5 : A discrepancy between the calculated position of the car and the actual one was detected | 5.4 | Positioning fault | Warning | A discrepancy between the calculated position of the car and the actual one was detected | A difference between the calculated position of the car and the real one was detected in correspondence of the activation of door zone sensor ZP (passing floor) | Check: 1) The correct positioning of the magnets 2) The operation of the magnetic pulsers 3) The distance between extreme contact and magnet | |
Fault 5 : A discrepancy between the calculated position of the car and the actual one was detected | 5.5 | Positioning fault | Warning | A discrepancy between the calculated position of the car and the actual one was detected | A difference between the calculated position of the car and the real one was detected in correspondence of the activation of door zone sensor ZP (passing floor) | Check: 1) The correct positioning of the magnets 2) The operation of the magnetic pulsers 3) The distance between extreme contact and magnet 4) The correct operation/connection of the encoder | The tolerance is up to 5 cm compared to the learning quota. |
Fault 5 : A discrepancy between the calculated position of the car and the actual one was detected | 5.6 | Positioning fault | Warning | A discrepancy between the calculated position of the car and the actual one was detected | A difference between the calculated position of the car and the real one was detected in correspondence of the activation of door zone sensor ZP (passing floor) | Check: 1) The correct positioning of the magnets 2) The operation of the magnetic pulsers 3) The distance between extreme contact and magnet 4) The correct operation/connection of the encoder | The tolerance is up to 5 cm compared to the learning quota. |
Fault 5 : A discrepancy between the calculated position of the car and the actual one was detected | 5.7 | Positioning fault | Warning | A discrepancy between the calculated position of the car and the actual one was detected | A difference between the calculated position of the car and the real one was detected in correspondence of the activation of door zone sensor ZP (stopping floor) | Check: 1) The correct positioning of the magnets 2) The operation of the magnetic pulsers 3) The distance between extreme contact and magnet | |
Fault 5 : A discrepancy between the calculated position of the car and the actual one was detected | 5.8 | Positioning fault | Warning | A discrepancy between the calculated position of the car and the actual one was detected | A difference between the calculated position of the car and the real one was detected in correspondence of the activation of door zone sensor ZP (stopping floor) | Check: 1) The correct positioning of the magnets 2) The operation of the magnetic pulsers 3) The distance between extreme contact and magnet 4) The correct operation/connection of the encoder | The tolerance is up to 5 cm compared to the learning quota. |
Fault 5 : A discrepancy between the calculated position of the car and the actual one was detected | 5.9 | Positioning fault | Warning | A discrepancy between the calculated position of the car and the actual one was detected | A difference between the calculated position of the car and the real one was detected in correspondence of the activation of door zone sensor ZP (stopping floor) | Check: 1) The correct positioning of the magnets 2) The operation of the magnetic pulsers 3) The distance between extreme contact and magnet 4) The correct operation/connection of the encoder | The tolerance is up to 5 cm compared to the learning quota. |
Fault 5 : A discrepancy between the calculated position of the car and the actual one was detected | 5.0 | Positioning fault | Warning | A discrepancy between the calculated position of the car and the actual one was detected | A difference between the calculated position of the car and the real one was detected in correspondence of the activation of one of the AGB/AGH limit switches. | Check: 1) The correct positioning of the magnets 2) The operation of the magnetic pulsers 3) The distance between extreme contact and magnet In case of DMG Rope Encoder 4) The correct operation/connection of the encoder | The tolerance is up to 5 cm compared to the learning quota. |
Fault 5 : A discrepancy between the calculated position of the car and the actual one was detected | 5.100 | Positioning fault | Warning | A discrepancy between the calculated position of the car and the actual one was detected | A difference between the calculated position of the car and the real one was detected in correspondence of the activation of door zone sensor ZP (passing floor) | Check: 1) The correct positioning of the magnets 2) The operation of the magnetic pulsers 3) The distance between extreme contact and magnet In case of DMG Rope Encoder 4) The correct operation/connection of the encoder | |
Fault 5 : A discrepancy between the calculated position of the car and the actual one was detected | 5.200 | Positioning fault | Warning | A discrepancy between the calculated position of the car and the actual one was detected | A difference between the calculated position of the car and the real one was detected in correspondence of the activation of door zone sensor ZP (stopping floor) | Check: 1) The correct positioning of the magnets 2) The operation of the magnetic pulsers 3) The distance between extreme contact and magnet In case of DMG Rope Encoder 4) The correct operation/connection of the encoder | |
Fault 6 : Wrong direction of travel | 6.0 | Direction fault | Alert | Wrong direction of travel | The controller detected the wrong direction of travel. | Check: In case of rope encoder 1) The direction of travel of the lift motor vs. the set direction (for example UP command vs. direction of car movement). The encoder value must increase if the lift goes UP (it must decrease in descent). This value is visible in the “Monitor Encoder” menu via PlayPad (https://dido.dmg.it/knowledge-base/controller-p40/#system-positioning-menu); 2) The clockwise / counter-clockwise configuration of the Encoder (https://dido.dmg.it/knowledge-base/controller-p40/#system-positioning-menu); 3) The AGH and AGB inputs (if they are activated in the opposite direction to the direction of travel of the lift) In case of magnet and magnetic switch counting system: 1) The direction of travel of the lift motor vs. the direction (for example UP command vs. direction of car movement). Check the correct activation of the input sensors of the FAI/FAS magnet and magnetic switch counting system (I/O status menu of the PlayPad https://dido.dmg.it/knowledge-base/controller-p40/#i-o-status-menu). 2) Counting with magnet and magnetic switch system (FAI/FAS): Installation and connection of the impulse switches. Check for any magnetization phenomena on the guides; 3) The AGH and AGB inputs (if they are activated in the opposite direction to the direction of travel of the lift) | |
Fault 6 : Wrong direction of travel | 6.1 | Direction fault | Alert | Wrong direction of travel | The controller detected the wrong direction of travel. | Check: 1) The direction of travel of the lift motor vs. the set direction (for example UP command vs. direction of car movement). The encoder value must increase if the lift goes UP (it must decrease in descent). This value is visible in the “Monitor Encoder” menu via PlayPad (https://dido.dmg.it/knowledge-base/controller-p40/#system-positioning-menu); 2) The clockwise / counter-clockwise configuration of the Encoder (https://dido.dmg.it/knowledge-base/controller-p40/#system-positioning-menu); 3) The AGH and AGB inputs (if they are activated in the opposite direction to the direction of travel of the lift) | |
Fault 6 : Wrong direction of travel | 6.2 | Direction fault | Alert | Wrong direction of travel | The controller detected the wrong direction of travel. | Check: 1) The direction of travel of the lift motor vs. the direction (for example UP command vs. direction of car movement). Check the correct activation of the input sensors of the FAI/FAS magnet and magnetic switch counting system (I/O status menu of the PlayPad https://dido.dmg.it/knowledge-base/controller-p40/#i-o-status-menu). 2) Counting with magnet and magnetic switch system (FAI/FAS): Installation and connection of the impulse switches. Check for any magnetization phenomena on the guides; 3) The AGH and AGB inputs (if they are activated in the opposite direction to the direction of travel of the lift) | |
Fault 7 : Safety chain point #3 is interrupted while the lift is not moving. All calls are deleted. | 7.0 | Safety 3 open with car stopped | Alert | Safety chain point #3 is interrupted while the lift is not moving. All calls are deleted. | A safety contact ahead of Point #3 (Parachute, final limit switch, overspeed governor contacts) is open while the lift is stopped. The car cannot move normally and calls are inhibited. | Check all contacts between the terminals: S35 – S36 (Top of Car) SC3 –SM4 (Controller) Check the contacts for the following safety devices: Safety Gear, Limit switches, Overspeed Governor | |
Fault 9 : Floor door fault: the safety chain is open (Point #6). The system will try to open and close automatic doors (maximum 3 attempts, after which all calls are canceled). In case of manual doors, after a few seconds all calls are canceled. | 9.5 | Door lock fault | Alert | Floor door fault: the safety chain is open (Point #6). The system will try to open and close automatic doors (maximum 3 attempts, after which all calls are canceled). In case of manual doors, after a few seconds all calls are canceled. | One of the safety contacts before point #6 is open when a call is registered. The problem is limited to the floor door where the lift is stopped and could be caused by: 1) Safety contacts connection 2) Mechanical door obstruction 3) Protection contacts (81-21 devices) | Check: 1) All contacts between the terminals SD2-SD3 and their connections 2) Obstructions of the door that may prevent closure at the floor indicated on PlayPad (POS) 3) The correct closing of floor door lock 4) In case of 81-21 devices, check its contacts in Normal mode operations 5) The correct functioning of the SM3 safety module: the red “OUT” LED must be on if both the green S1 and S2 LEDs are on | |
Fault 9 : Car door fault: the safety chain is open (Point #6). The system will try to open and close automatic doors (maximum 3 attempts, after which all calls are canceled). In case of manual doors, after a few seconds all calls are canceled. | 9.6 | Door lock fault | Alert | Car door fault: the safety chain is open (Point #6). The system will try to open and close automatic doors (maximum 3 attempts, after which all calls are canceled). In case of manual doors, after a few seconds all calls are canceled. | One of the safety contacts before point #6 is open when a call is registered. The problem is limited to the car door and could be caused by: 1) Safety contacts connection 2) Mechanical door obstruction 3) Floor door lock not closed 4) Protection contacts (81-21 devices) | Check: 1) All contacts between the terminals S35 – S36 (Top of car), SC4 – SC5 and their connection (Controller) 2) If an object obstructs the closing of the door to the indicated floor on PlayPad (POS) 3) The correct closing of floor door locks 4) In case of 81-21 devices, check its contacts in Normal mode operations | |
Fault 10 : Door A did not open within the set time (10s default) and is therefore considered as open. | 10.0 | Door A opening slippage | Warning | Door A did not open within the set time (10s default) and is therefore considered as open. | 1) Door limit switch (FOA) doesn’t detect correct door closure 2) The door operator doesn’t function 3) The controller doesn’t provide opening command (ROA) | Check: 1) Door open limit switch (FOA) and its wiring (FOx on MOT3 board for three-phase ports/AUTO board for regulated door operators, JDA on TOC board); setting (by PlayPad, see https://dido.dmg.it/it/knowledge-base/controller-p40/#doors-menu) 2) Door operator power supply (MOT3 board for three-phase ports/AUTO board for regulated door operators) and fuses; 3) Door open contactors ROA (menu I/O PlayPad, see https://dido.dmg.it/it/knowledge-base/controller-p40/#i-o-status-menu) | Door with limit switch (set https://dido.dmg.it/knowledge-base/controller-p40/#doors-menu). Door open limit switch FOA and door open contactors ROA status are viewable via Playpad in I/O status menu, Playboard in/out page 3 |
Fault 11 : Door B did not open within the set time (10s default) and is therefore considered as open. | 11.0 | Door B opening slippage | Warning | Door B did not open within the set time (10s default) and is therefore considered as open. | 1) Door limit switch (FOB) doesn’t detect correct door closure 2) The door operator doesn’t function 3) The controller doesn’t provide opening command (ROB) | Check: 1) Door open limit switch (FOB) and its wiring (FOx on MOT3 board for three-phase ports/AUTO board for regulated door operators, JDA on TOC board); setting (by PlayPad, see programmazione (tramite PlayPad, vedere https://dido.dmg.it/it/knowledge-base/controller-p40/#doors-menu) 2) Door operator power supply (MOT3 board for three-phase ports/AUTO board for regulated door operators) and fuses; 3) Door open contactors ROB (menu I/O PlayPad, see https://dido.dmg.it/it/knowledge-base/controller-p40/#i-o-status-menu) | Door with limit switch (set https://dido.dmg.it/knowledge-base/controller-p40/#doors-menu). Door open limit switch FOA and door open contactors ROA status are viewable via Playpad in I/O status menu, Playboard in/out page 3 |
Fault 12 : Safety chain point #3 is interrupted during travel. All calls are deleted. Led SE3 on PlayPad is OFF. | 12.0 | Safety 3 open during travel | Warning | Safety chain point #3 is interrupted during travel. All calls are deleted. Led SE3 on PlayPad is OFF. | A safety contact ahead of Point #3 (parachute, final limit switch, overspeed governor contacts) is open while the lift is running. The car is blocked and calls are inhibited. | Check all contacts between the terminals: S35 – S36 (Top of Car) SC3 –SM4 (Controller) Check the contacts for the following safety devices: Safety Gear, Limit switches, Overspeed Governor | |
Fault 13 : Engine temperature too high (TH1 sensor). | 13.1 | Motor temperature sensor | Warning | Engine temperature too high (TH1 sensor). | High temperature on the geared/gearless machine (or other device where the TH1 thermal probe is connected) | Check: 1) Input TH1; 2) Sensor connections; 3) Status of the thermal probe applied on the machine (see PlayPad in I/O status menu, Playboard in/out page 1) | |
Fault 13 : Hydro pump temperature too high (TH2 sensor). | 13.2 | Motor temperature sensor | Warning | Hydro pump temperature too high (TH2 sensor). | High temperature on the hydro pump or oil tank (or other device where the TH2 thermal probe is connected). | Check: 1) Input TH2; 2) Sensor connections; 3) Status of the thermal probe applied on the oil pump (see PlayPad in I/O status menu, Playboard in/out page 1) | |
Fault 13 : Engine / Hydro pump temperature too high (Both TH1 and TH2 sensors are activated). | 13.3 | Motor temperature sensor | Warning | Engine / Hydro pump temperature too high (Both TH1 and TH2 sensors are activated). | High temperature on both thermal probes applied to the hydro pump and oil tank (or other devices where the TH1/ TH2 thermal probes are connected). | Check: 1) Input TH1 and TH2; 2) Sensor connections; 3) Status of the thermal probes (see PlayPad in I/O status menu, Playboard in/out page 1) | |
Fault 13 : Door operator temperature too high | 13.10 | Motor temperature sensor | Warning | Door operator temperature too high | The thermal input on the TOC board is activated due to excessive temperature on the door motor. | Check: 1) Input M19 on TOC board | |
Fault 14 : Fault in the Eprom parameters memory | 14.0 | Parameters memory | Warning | Fault in the Eprom parameters memory | Parameters memory | Reset, re-enter and record all parameters | |
Fault 15 : Blocking Error! Point #3 of the safety chain has remained open for more than 1.5 seconds. All floor and car calls are inhibited. A specific reset of the system is required (the system will carry out a reset procedure by moving the car to the highest floor). | 15.1 | Final limit switch | Alert + Reset | Blocking Error! Point #3 of the safety chain has remained open for more than 1.5 seconds. All floor and car calls are inhibited. A specific reset of the system is required (the system will carry out a reset procedure by moving the car to the highest floor). | The cabin has reached a final limit switch, or the speed limiter and/or the parachute has intervened. In all cases, point #3 of the safety chain remained open for a time >1.5sec and the system is blocked. A specific reset procedure is required, even after the safety chain has been closed. | 1) Release the final limit switch (or Safety Gear or OSG) closing the safety chain (SE3) and cancel fault in the PlayPad “Faults” Menu (Reset SE3). 2) Check Positioning System; 3) Check Brake Hold | |
Fault 15 : Blocking Error! Point #3 of the safety chain has remained open for more than 1.5 seconds. All floor and car calls are inhibited. A specific reset of the system is required (the system will carry out a reset procedure by moving the car to the lowest floor). | 15.2 | Final limit switch | Alert + Reset | Blocking Error! Point #3 of the safety chain has remained open for more than 1.5 seconds. All floor and car calls are inhibited. A specific reset of the system is required (the system will carry out a reset procedure by moving the car to the lowest floor). | The cabin has reached a final limit switch, or the speed limiter and/or the parachute has intervened. In all cases, point #3 of the safety chain remained open for a time >1.5sec and the system is blocked. A specific reset procedure is required, even after the safety chain has been closed. | 1) Release the final limit switch (or Safety Gear or OSG) closing the safety chain (SE3) and cancel fault in the PlayPad “Faults” Menu (Reset SE3). 2) Check Positioning System; 3) Check Valve circuit | |
Fault 15 : Blocking Error! Point #3 of the safety chain has remained open for more than 1.5 seconds. All floor and car calls are inhibited. A specific reset of the system is required (the system will carry out a reset procedure by moving the car to the highest floor). | 15.0 | Final limit switch | Alert + Reset | Blocking Error! Point #3 of the safety chain has remained open for more than 1.5 seconds. All floor and car calls are inhibited. A specific reset of the system is required (the system will carry out a reset procedure by moving the car to the highest floor). | The cabin has reached a final limit switch, or the speed limiter and/or the parachute has intervened. In all cases, point #3 of the safety chain remained open for a time >1.5sec and the system is blocked. A specific reset procedure is required, even after the safety chain has been closed. | 1) Release the final limit switch (or Safety Gear or OSG) closing the safety chain (SE3) and cancel fault in the PlayPad “Faults” Menu (Reset SE3). 2) Check Positioning System; 3) In case of Electric Controller, check Brake Hold. In case of Hydraulic Controller, check Valve circuit | |
Fault 16 : One or more fire detection sensors are active (open). | 16.0 | Fire detection | Warning | One or more fire detection sensors are active (open). | If there are fire detection sensors installed in the building and connected to the controller, this fault indicates there is a fire in progress in one or more floors of the building (or the fire sensor(s) is (are) not functioning). | For serial controller, check: – The inputs POM and CPOM on the BDU through the PlayPad (see PlayPad in I/O status menu, Playboard in/out page 4) – The correct functioning of the fire sensor(s) For parallel controller, check: – The input status on 16 I/O board in the relevant PlayPad menu (see PlayPad in I/O status menu, AUX board) – The correct functioning of the fire sensor(s) | The behavior of the controller upon fire detection can be programmed via PlayPad (“Special functions” menu, see https://dido.dmg.it/knowledge-base/controller-p40/#special-features-menu): – “Fire detection” on YES: a) If the lift is on a different floor than the one where the fire was detected, all calls logged to/from this floor are canceled. b) If the lift is at the floor where the fire was detected, the controller stops the door opening, closes doors (if open upon fire detection), and sends the elevator car to a safe floor previously set. – “EN8173” to YES (Fire evacuation procedure). The following evacuation rule is applied: a) (If the fire detection is not active on the Main Floor) the car is moved to Main Floor. b) The car is moved to an alternative floor, where the fire sensor is not activated |
Fault 16 : One or more fire detection sensors are active (open). | 16.1 | Fire detection | Warning | One or more fire detection sensors are active (open). | If there are fire detection sensors installed in the building and connected to the controller, this fault indicates there is a fire in progress in one or more floors of the building (or the fire sensor(s) is (are) not functioning). | Check: – The inputs POM and CPOM on the BDU through the PlayPad (see PlayPad in I/O status menu, Playboard in/out page 4) – The correct functioning of the fire sensor(s) | The behavior of the controller upon fire detection can be programmed via PlayPad (“Special functions” menu, see https://dido.dmg.it/knowledge-base/controller-p40/#special-features-menu): – “Fire detection” on YES: a) If the lift is on a different floor than the one where the fire was detected, all calls logged to/from this floor are canceled. b) If the lift is at the floor where the fire was detected, the controller stops the door opening, closes doors (if open upon fire detection), and sends the elevator car to a safe floor previously set. – “EN8173” to YES (Fire evacuation procedure). The following evacuation rule is applied: a) (If the fire detection is not active on the Main Floor) the car is moved to Main Floor. b) The car is moved to an alternative floor, where the fire sensor is not activated |
Fault 16 : One or more fire detection sensors are active (open). | 16.2 | Fire detection | Warning | One or more fire detection sensors are active (open). | If there are fire detection sensors installed in the building and connected to the controller, this fault indicates there is a fire in progress in one or more floors of the building (or the fire sensor(s) is (are) not functioning). | Check: – The input status on 16 I/O board in the relevant PlayPad menu (see PlayPad in I/O status menu, AUX board) – The correct functioning of the fire sensor(s) | The behavior of the controller upon fire detection can be programmed via PlayPad (“Special functions” menu, see https://dido.dmg.it/knowledge-base/controller-p40/#special-features-menu): – “Fire detection” on YES: a) If the lift is on a different floor than the one where the fire was detected, all calls logged to/from this floor are canceled. b) If the lift is at the floor where the fire was detected, the controller stops the door opening, closes doors (if open upon fire detection), and sends the elevator car to a safe floor previously set. – “EN8173” to YES (Fire evacuation procedure). The following evacuation rule is applied: a) (If the fire detection is not active on the Main Floor) the car is moved to Main Floor. b) The car is moved to an alternative floor, where the fire sensor is not activated |
Fault 17 : Safety chain point #4 is interrupted during travel. Landing calls and the elevator car movements are deleted On the PlayPad Led SE4 is off. | 17.0 | Safety 4 open during travel | Alert | Safety chain point #4 is interrupted during travel. Landing calls and the elevator car movements are deleted On the PlayPad Led SE4 is off. | Safety 4 open during travel. A safety contact ahead of Point #4 (Floor preliminary locks) is open during travel. The car cannot move normally and calls are inhibited. | Check all contacts between the terminals: SD1 and SD2 (Preliminaries floor doors). | |
Fault 18 : Unexpected opening of a safety contact of one of the landing doors during travel (point #5 of the safety chain). Calls are cancelled. | 18.5 | Floor door contact open | Alert | Unexpected opening of a safety contact of one of the landing doors during travel (point #5 of the safety chain). Calls are cancelled. | A safety contact ahead of Point #5 (Floor doors) is open during travel, prossibly due to a mechanical matching problem between car door and floor foor. The car cannot move normally and calls are inhibited | Check all contacts between the terminals: SD2 and SD3 | |
Fault 18 : Unexpected opening of one of the safety contacts ahead of point #6 during travel. Calls are cancelled. | 18.6 | Safety 6 open during travel | Alert | Unexpected opening of one of the safety contacts ahead of point #6 during travel. Calls are cancelled. | A safety contact ahead of #6 (car doors or reduced pit/headroom protection devices) is open during travel. The car cannot move normally and calls are inhibited | Check all contacts between the terminals: SC4 and SC5 | |
Fault 19 : Motherboard power below 17V during the movement | 19.0 | Low tension during travel | Alert | Motherboard power below 17V during the movement | Main power Input | Check: – The network, the supply voltage to the transformer primary, the presence of 24V and the circuit absorption. The voltage and current intensity values can be viewed using the PlayPad in the “I/O status” menu, “Analogic” page (https://dido.dmg.it/knowledge-base/controller-p40/#i-o-status-menu) | This fault disappears when the 24V is restored |
Fault 19 : Motherboard power below 17V during the movement | 19.1 | Low tension during travel | Alert | Motherboard power below 17V during the movement | Overcurrent on VCAB (car circuit) | Check: – The network, the supply voltage to the transformer primary, the presence of 24V and the circuit absorption. The voltage and current intensity values can be viewed using the PlayPad in the “I/O status” menu, “Analogic” page (https://dido.dmg.it/knowledge-base/controller-p40/#i-o-status-menu) | This fault disappears when the 24V is restored |
Fault 19 : Motherboard power below 17V during the movement | 19.2 | Low tension during travel | Alert | Motherboard power below 17V during the movement | Overcurrent on VMR (floor circuit) | Check: – The network, the supply voltage to the transformer primary, the presence of 24V and the circuit absorption. The voltage and current intensity values can be viewed using the PlayPad in the “I/O status” menu, “Analogic” page (https://dido.dmg.it/knowledge-base/controller-p40/#i-o-status-menu) | This fault disappears when the 24V is restored |
Fault 19 : Motherboard power below 17V during the movement | 19.3 | Low tension during travel | Alert | Motherboard power below 17V during the movement | Short Circuit on VCAB (car circuit) | Check: – The network, the supply voltage to the transformer primary, the presence of 24V and the circuit absorption. The voltage and current intensity values can be viewed using the PlayPad in the “I/O status” menu, “Analogic” page (https://dido.dmg.it/knowledge-base/controller-p40/#i-o-status-menu) | This fault disappears when the 24V is restored |
Fault 19 : Motherboard power below 17V during the movement | 19.4 | Low tension during travel | Alert | Motherboard power below 17V during the movement | Short Circuit on VMR (floor circuit) | Check: – The network, the supply voltage to the transformer primary, the presence of 24V and the circuit absorption. The voltage and current intensity values can be viewed using the PlayPad in the “I/O status” menu, “Analogic” page (https://dido.dmg.it/knowledge-base/controller-p40/#i-o-status-menu) | This fault disappears when the 24V is restored |
Fault 19 : Missing 230V during the movement | 19.230 | Low tension during travel | Alert | Missing 230V during the movement | Missing 230 V, controller is powered with batteries | Check: – Backup circuit (R230) if present or shunt on J8 of CHAR board | This fault disappears when the 230V is restored |
Fault 20 : The cabin suddenly stopped while travelling, probably due to a micro-interruption in the safety circuit. The motor contactor (CCO) is open. However, it is possible to resume normal operation by making a new call. | 20.100 | Travel interrupted | Alert | The cabin suddenly stopped while travelling, probably due to a micro-interruption in the safety circuit. The motor contactor (CCO) is open. However, it is possible to resume normal operation by making a new call. | A physical or electrical micro interruption of the safety chain during the movement of the lift car may have caused the opening of the motor contactor (CCO signal) while the running commands were active (RMO for upward run or RDE for downward run). The lift car has stopped. | Check: – Preliminary contacts and door locks at the floor indicated on the Playpad screen; – Car door contacts; – The supply voltage of the safety circuit; – The correct operation of the contactor (possible false contacts, wiring and oxidation of contacts). | |
Fault 20 : The cabin suddenly stopped while travelling, probably due to a micro-interruption in the safety circuit. The brake contactor (CCOB) is open. However, it is possible to resume normal operation by making a new call. | 20.200 | Travel interrupted | Alert | The cabin suddenly stopped while travelling, probably due to a micro-interruption in the safety circuit. The brake contactor (CCOB) is open. However, it is possible to resume normal operation by making a new call. | A physical or electrical micro interruption of the safety chain during the movement of the lift car may have caused the opening of the brake contactor (CCOB signal) while the running commands were active (RMO for upward run or RDE for downward run). The lift car has stopped. | Check: – Preliminary contacts and door locks at the floor indicated on the Playpad screen; – Car door contacts; – The supply voltage of the safety circuit; – The correct operation of the contactor (possible false contacts, wiring and oxidation of contacts). | |
Fault 20 : The cabin suddenly stopped while travelling, probably due to a micro-interruption in the safety circuit. The motor contactor (CM1) is open. However, it is possible to resume normal operation by making a new call. | 20.110 | Travel interrupted | Alert | The cabin suddenly stopped while travelling, probably due to a micro-interruption in the safety circuit. The motor contactor (CM1) is open. However, it is possible to resume normal operation by making a new call. | A physical or electrical micro interruption of the safety chain during the movement of the lift car may have caused the opening of the CM1 (YBRK signal for direct start, delta star or VVVF Hydro, CCO signal for SoftStarter) while the running commands were active (RMO for upward run or RDE for downward run). The lift car has stopped. | Check: – Preliminary contacts and door locks at the floor indicated on the Playpad screen; – Car door contacts; – The supply voltage of the safety circuit; – The correct operation of the contactor (possible false contacts, wiring and oxidation of contacts). | |
Fault 20 : The cabin suddenly stopped while travelling, probably due to a micro-interruption in the safety circuit. The motor contactor (CM2) is open. However, it is possible to resume normal operation by making a new call. | 20.120 | Travel interrupted | Alert | The cabin suddenly stopped while travelling, probably due to a micro-interruption in the safety circuit. The motor contactor (CM2) is open. However, it is possible to resume normal operation by making a new call. | A physical or electrical micro interruption of the safety chain during the movement of the lift car may have caused the opening of the CM2 (CCO signal for direct start, delta star or VVVF Hydro) while the running commands were active (RMO for upward run or RDE for downward run). The lift car has stopped. | Check: – Preliminary contacts and door locks at the floor indicated on the Playpad screen; – Car door contacts; – The supply voltage of the safety circuit; – The correct operation of the contactor (possible false contacts, wiring and oxidation of contacts). | |
Fault 20 : The cabin suddenly stopped while travelling, probably due to a micro-interruption in the safety circuit. The motor contactor (CM3) is open. However, it is possible to resume normal operation by making a new call. | 20.130 | Travel interrupted | Alert | The cabin suddenly stopped while travelling, probably due to a micro-interruption in the safety circuit. The motor contactor (CM3) is open. However, it is possible to resume normal operation by making a new call. | A physical or electrical micro interruption of the safety chain during the movement of the lift car may have caused the opening of the CM3 (CCO signal for star-delta starting) while the running commands were active (RMO for upward run or RDE for downward run). The lift car has stopped. | Check: – Preliminary contacts and door locks at the floor indicated on the Playpad screen; – Car door contacts; – The supply voltage of the safety circuit; – The correct operation of the contactor (possible false contacts, wiring and oxidation of contacts). | |
Fault 20 : The cabin suddenly stopped while travelling, probably due to a micro-interruption in the safety circuit. The motor contactor (CCO) is open. However, it is possible to resume normal operation by making a new call. | 20.140 | Travel interrupted | Alert | The cabin suddenly stopped while travelling, probably due to a micro-interruption in the safety circuit. The motor contactor (CCO) is open. However, it is possible to resume normal operation by making a new call. | A physical or electrical micro interruption of the safety chain during the movement of the lift car may have caused the opening of the CM2 SoftStarter motor contactor (YBRK signal for Softstarter) while the running commands were active (RMO for upward run or RDE for downward run). The lift car has stopped. | Check: – Preliminary contacts and door locks at the floor indicated on the Playpad screen; – Car door contacts; – The supply voltage of the safety circuit; – The correct operation of the contactor (possible false contacts, wiring and oxidation of contacts). | |
Fault 21 : Blocking error! After the run command, the CCO control input of the motor contactor remained closed during the lift start sequence | 21.100 | CCO Input blocked | Alert + Reset | Blocking error! After the run command, the CCO control input of the motor contactor remained closed during the lift start sequence | The control circuit of the run contactors (motor input CCO, NC at standstill) does not change state after the run command has been given. Contact lost on CCO circuit or CTB motor contactor faulty | Check: 1) The activation of relay RM1 (see circuit diagram); 2) The series of the auxiliary contacts (NC) of the contactors and the other wires in series in the CCO circuit 3) The wiring of the CCO circuit as shown in the circuit diagrams 4) The CCO input on the motherboard (connectors J22 or J23 or J14) | The status of the CCO input can be viewed via Playpad in the I/O status menu, Playboard in/out page 2 |
Fault 21 : Blocking error! After the run command, the CCOB control input of the motor contactor remained closed during the lift start sequence | 21.200 | CCO Input blocked | Alert + Reset | Blocking error! After the run command, the CCOB control input of the motor contactor remained closed during the lift start sequence | The run contactor control circuit (CCOB input, NC at standstill) does not change state after the run command has been given | For VVVF controller Check: – Contactor CTB1 (also CTB2 if present); – RBRK relay activation. For hydraulic controller Check: – Valve contactors CV1, CV2, CV3, CV4, CV5, CVC (if present). | |
Fault 21 : Blocking error! During the start sequence of the system, the control input YRBK (for Direct Start option) or CCO (for Star Delta and Soft Starter option) of the motor contactor remained closed after the run command. | 21.110 | CCO Input blocked | Alert + Reset | Blocking error! During the start sequence of the system, the control input YRBK (for Direct Start option) or CCO (for Star Delta and Soft Starter option) of the motor contactor remained closed after the run command. | The run contactor control circuit (YBRK or CCO motor input, NC at standstill) does not change state after the run command has been given. Contact lost on YBRK circuit or CM1 motor contactor faulty (Only for Direct option) Contact lost on CCO circuit or motor contactor CM1 faulty (Only for Star Delta option) Lost contact on CCO circuit or failed CM1 motor contactor (Only for Soft Starter option) | Check: 1) The auxiliary contact set (NC) of the motor contactors and the other wires in series in the CCO circuit and the YBRK circuit 2) The wiring of the CCO circuit and the YBRK circuit as shown in the circuit diagrams. 3) The CCO input on the COIL board (connectors J2 or JM1) or on connector J22 on the motherboard; 4) The YBRK input of connector J23 on the motherboard. | The status of the CCO input can be viewed via Playpad in the I/O status menu, Playboard in/out page 2. Input status YBRK is displayed via Playpad in the I/O status menu, Playboard in/out page 2 |
Fault 21 : Blocking error! During the system start sequence, the CCO control input (for Direct Start and Star Delta option) of the motor contactor remained closed after the run command. | 21.120 | CCO Input blocked | Alert + Reset | Blocking error! During the system start sequence, the CCO control input (for Direct Start and Star Delta option) of the motor contactor remained closed after the run command. | The run contactor control circuit (CCO motor input, NC at standstill) does not change state after the run command has been given. Contact lost on CCO circuit or motor contactor CM2 faulty (Only for Star Delta and Direct option) | Check: 1) The auxiliary contact set (NC) of the motor contactors and the other cables in series in the CCO circuit 2) The wiring of the CCO circuit as shown in the circuit diagrams. 3) The CCO input on the COIL board (connectors J2 or JM1) or on connector J22 on the motherboard; | The status of the CCO input can be viewed via Playpad in the I/O status menu, Playboard in/out page 2. |
Fault 21 : Blocking error! During the system start sequence, the CCO control input (for Star Delta option) of the motor contactor remained closed after the run command. | 21.130 | CCO Input blocked | Alert + Reset | Blocking error! During the system start sequence, the CCO control input (for Star Delta option) of the motor contactor remained closed after the run command. | The run contactor control circuit (CCO motor input, NC at standstill) does not change state after the run command has been given. Contact lost on CCO circuit or motor contactor CM3 faulty (Only for Star Delta option) | Check: 1) The auxiliary contact set (NC) of the motor contactors and the other cables in series in the CCO circuit 2) The wiring of the CCO circuit as shown in the circuit diagrams. 3) The CCO input on the COIL board (connectors J2 or JM1) or on connector J22 on the motherboard; | The status of the CCO input can be viewed via Playpad in the I/O status menu, Playboard in/out page 2. |
Fault 21 : Blocking error! During the system start sequence, the YBRK control input (for Soft Starter option) of the motor contactor remained closed after the run command. | 21.140 | CCO Input blocked | Alert + Reset | Blocking error! During the system start sequence, the YBRK control input (for Soft Starter option) of the motor contactor remained closed after the run command. | The run contactor control circuit (YBRK motor input, NC at standstill) does not change state after the run command has been given. Contact lost on YBRK circuit or motor contactor CM2 faulty (Only for Star Delta option) | Check: 1) The auxiliary contact set (NC) of the motor contactors and the other cables in series in the YBRK circuit 2) The wiring of the YBRK circuit as shown in the circuit diagrams. 3) The YBRK input of connector J23 on the motherboard. | The status of the YBRK input can be viewed via Playpad in the I/O status menu, Playboard in/out page 2 |
Fault 21 : The error appears when the drive is not controlling the brake contactor. This is then controlled by the switchgear. | 21.250 | CCO Input blocked | Alert | The error appears when the drive is not controlling the brake contactor. This is then controlled by the switchgear. | CTB1 / CTB2 input not activated | Verify: – Parameterisation of Y5C/A (brake output) via PlayPad; – Parameter L80 (closed loop always equal to 1, if set to 2 check activation current in parameter L81.); – Inverter activation sequence (ENABLE-> DIRECTION-> SPEED). | |
Fault 22 : Motherboard power supply below 17V at stop | 22.0 | Low tension at stop | Alert | Motherboard power supply below 17V at stop | Main power Input | Check: – The network, the supply voltage to the transformer primary, the presence of 24V and the circuit absorption. The voltage and current intensity values can be viewed using the PlayPad in the “I/O status” menu, the “Analogic” page (https://dido.dmg.it/knowledge-base/controller-p40/#i-o-status-menu) | This fault disappears when the 24V is restored |
Fault 22 : Motherboard power supply below 17V at stop | 22.1 | Low tension at stop | Alert | Motherboard power supply below 17V at stop | Overcurrent on VCAB (car circuit) | Check: – The network, the supply voltage to the transformer primary, the presence of 24V and the circuit absorption. The voltage and current intensity values can be viewed using the PlayPad in the “I/O status” menu, the “Analogic” page (https://dido.dmg.it/knowledge-base/controller-p40/#i-o-status-menu) | This fault disappears when the 24V is restored |
Fault 22 : Motherboard power supply below 17V at stop | 22.2 | Low tension at stop | Alert | Motherboard power supply below 17V at stop | Overcurrent on VMR (floor circuit) | Check: – The network, the supply voltage to the transformer primary, the presence of 24V and the circuit absorption. The voltage and current intensity values can be viewed using the PlayPad in the “I/O status” menu, the “Analogic” page (https://dido.dmg.it/knowledge-base/controller-p40/#i-o-status-menu) | This fault disappears when the 24V is restored |
Fault 22 : Motherboard power supply below 17V at stop | 22.3 | Low tension at stop | Alert | Motherboard power supply below 17V at stop | Short Circuit on VCAB (car circuit) | Check: The network, the supply voltage to the transformer primary, the presence of 24V and the circuit absorption. The voltage and current intensity values can be viewed using the PlayPad in the “I/O status” menu, the “Analogic” page (https://dido.dmg.it/knowledge-base/controller-p40/#i-o-status-menu) | This fault disappears when the 24V is restored |
Fault 22 : Motherboard power supply below 17V at stop | 22.4 | Low tension at stop | Alert | Motherboard power supply below 17V at stop | Short Circuit on VMR (floor circuit) | Check: – The network, the supply voltage to the transformer primary, the presence of 24V and the circuit absorption. The voltage and current intensity values can be viewed using the PlayPad in the “I/O status” menu, the “Analogic” page (https://dido.dmg.it/knowledge-base/controller-p40/#i-o-status-menu) | This fault disappears when the 24V is restored |
Fault 22 : Missing 230V during the movement | 22.230 | Low tension at stop | Alert | Missing 230V during the movement | Missing 230 V, controller is powered with batteries | Check: – Backup circuit (R230) if present or shunt on J8 of CHAR board | This fault disappears when the 230V is restored |
Fault 23 : The bottom reset sensor (AGB) is unexpectedly open while the car is away from the lower floor. Downward calls have been canceled and travel can only continue upwards. | 23.100 | Reset sensor fault (AGB) | Alert | The bottom reset sensor (AGB) is unexpectedly open while the car is away from the lower floor. Downward calls have been canceled and travel can only continue upwards. | The AGB reset contact (NC) is open when it should remain closed. | Check: 1) The status of the AGB contact (PlayPad, I/O status menu, Playboard I/O page 7, https://dido.dmg.it/it/knowledge-base/controller-p40/#i-o-status-menu) and the AGB circuit wiring; 2) The position of the magnets and the reset switch | |
Fault 23 : The bottom reset sensor (AGB) remained closed with the car at the lower floor. The lift is temporarily blocked. | 23.200 | Reset sensor fault (AGB) | Alert | The bottom reset sensor (AGB) remained closed with the car at the lower floor. The lift is temporarily blocked. | The AGB (NC) contact remained closed with the car at the lowest floor. | Check: 1) The status of the AGB contact (PlayPad, I/O status menu, Playboard I/O page 7, https://dido.dmg.it/it/knowledge-base/controller-p40/#i-o-status-menu) and the AGB circuit wiring; 2) The position of the magnets and the reset switch | |
Fault 24 : The bottom reset sensor (AGH) is unexpectedly open while the car is away from the upper floor. Upward calls have been canceled and travel can only continue downwards. | 24.100 | Reset sensor fault (AGH) | Alert | The bottom reset sensor (AGH) is unexpectedly open while the car is away from the upper floor. Upward calls have been canceled and travel can only continue downwards. | The AGH reset contact (NC) is open when it should remain closed. | Check: 1) The status of the AGH contact (PlayPad, I/O status menu, Playboard I/O page 7, https://dido.dmg.it/it/knowledge-base/controller-p40/#i-o-status-menu) and the AGH circuit wiring; 2) The position of the magnets and magnetic switch | |
Fault 24 : The top reset sensor (AGH) remained closed with the car at the upper floor. The lift is temporarily blocked. | 24.200 | Reset sensor fault (AGH) | Alert | The top reset sensor (AGH) remained closed with the car at the upper floor. The lift is temporarily blocked. | The AGH (NC) contact remained closed with the car at the top floor. | Check: 1) The status of the AGH contact (PlayPad, I/O status menu, Playboard I/O page 7, https://dido.dmg.it/it/knowledge-base/controller-p40/#i-o-status-menu) and the AGH circuit wiring; 2) The position of the magnets and reset switch | |
Fault 25 : Both the high and low reset sensor contacts (AGB and AGH) are open while the car is away from the extreme floors. The lift is temporarily blocked. | 25.0 | AGH and AGB simultaneously | Alert | Both the high and low reset sensor contacts (AGB and AGH) are open while the car is away from the extreme floors. The lift is temporarily blocked. | Inputs AGB / AGH opened simultaneously. The lift is blocked. When one of the two contacts is closed, the system performs a reset procedure. | Check the condition of AGH and AGB contacts and their wiring. When one of the two contacts is closed, the system performs a reset manoeuvre. | |
Fault 26 : No change in the beam status for motion sensors (or floor) for more than planned during car travel. | 26.0 | Upward travel time | Alert + Reset | No change in the beam status for motion sensors (or floor) for more than planned during car travel. | Problem on FAI FAS input (no changing of inputs for time longer than “Running time” parameter | Check: – Contactors, brake, motor power supply, FAI/FAS sensors (or ENCODER); – “X1” and “12” inputs of the VVVF; – Anti-slippage test:See Annex II – Test and measures | |
Fault 26 : No change in the beam status for motion sensors (or floor) for more than planned during car travel. | 26.100 | Upward travel time | Alert + Reset | No change in the beam status for motion sensors (or floor) for more than planned during car travel. | Problem on encoder channel | Check: – Contactors, brake, motor power supply, FAI/FAS sensors (or ENCODER); – “X1” and “12” inputs of the VVVF; – Anti-slippage test:See Annex II – Test and measures | |
Fault 26 : No change in the beam status for motion sensors (or floor) for more than planned during car travel. | 26.200 | Upward travel time | Alert + Reset | No change in the beam status for motion sensors (or floor) for more than planned during car travel. | No changing of Door Zone input (ZP) for time longer than “Running time” parameter | Check: – Contactors, brake, motor power supply, FAI/FAS sensors (or ENCODER); – “X1” and “12” inputs of the VVVF; – Anti-slippage test:See Annex II – Test and measures | |
Fault 27 : No change in the beam status for motion sensors (or floor) for more than planned during car travel. | 27.0 | Downward travel time | Alert + Reset | No change in the beam status for motion sensors (or floor) for more than planned during car travel. | Problem on FAI FAS input (no changing of inputs for time longer than “Running time” parameter | Check: – Contactors, brake, motor power supply, FAI/FAS sensors (or ENCODER); – “X1” and “12” inputs of the VVVF; – Anti-slippage test:See Annex II – Test and measures | |
Fault 27 : No change in the beam status for motion sensors (or floor) for more than planned during car travel. | 27.100 | Downward travel time | Alert + Reset | No change in the beam status for motion sensors (or floor) for more than planned during car travel. | Problem on encoder channel | Check: – Contactors, brake, motor power supply, FAI/FAS sensors (or ENCODER); – “X1” and “12” inputs of the VVVF; – Anti-slippage test:See Annex II – Test and measures | |
Fault 27 : No change in the beam status for motion sensors (or floor) for more than planned during car travel. | 27.200 | Downward travel time | Alert + Reset | No change in the beam status for motion sensors (or floor) for more than planned during car travel. | No changing of Door Zone input (ZP) for time longer than “Running time” parameter | Check: – Contactors, brake, motor power supply, FAI/FAS sensors (or ENCODER); – “X1” and “12” inputs of the VVVF; – Anti-slippage test:See Annex II – Test and measures | |
Fault 28 : Door A slips during closing and has not completed closing within the set time (normally: 10s). After three unsuccessful attempts, the calls were cancelled. | 28.0 | Door A closing slippage | Alert | Door A slips during closing and has not completed closing within the set time (normally: 10s). After three unsuccessful attempts, the calls were cancelled. | If door A does not close properly, it is possible that: 1) There is a false contact on the door limit switch (FFA / FFx) 2) The power supply to the door operator is not adequate 3) No RFA opening command is provided 4) The closing time set is too short | Check: 1) Door close limit switch (FFA) and its wiring (FFx on MOT3 board for three-phase ports/AUTO board for regulated door operators, JDA on TOC board); setting (by PlayPad, see programmazione (tramite PlayPad, vedere https://dido.dmg.it/it/knowledge-base/controller-p40/#doors-menu) 2) Door operator power supply (MOT3 board for three-phase ports/AUTO board for regulated door operators) and fuses; 3) Door close contactors RFA (menu I/O PlayPad, see https://dido.dmg.it/it/knowledge-base/controller-p40/#i-o-status-menu); 4) Set a different time (https://dido.dmg.it/it/knowledge-base/controller-p40/#doors-menu) | Door with limit switch (set https://dido.dmg.it/knowledge-base/controller-p40/#doors-menu) Door open limit switch FFA and door open contactors RFA status are viewable via Playpad in I/O status menu, Playboard in/out page 3 |
Fault 29 : Door B slips during closing and has not completed closing within the set time (normally: 10s). After three unsuccessful attempts, the calls were cancelled. | 29.0 | Door B closing slippage | Alert | Door B slips during closing and has not completed closing within the set time (normally: 10s). After three unsuccessful attempts, the calls were cancelled. | If door B does not close properly, it is possible that: 1) There is a false contact on the door limit switch (FFB / FFx) 2) The power supply to the door operator is not adequate 3) No RFA opening command is provided 4) The closing time set is too short | Check: 1) Door close limit switch (FFB) and its wiring (FFx on MOT3 board for three-phase ports/AUTO board for regulated door operators, JDA on TOC board); setting (by PlayPad, see programmazione (tramite PlayPad, vedere https://dido.dmg.it/it/knowledge-base/controller-p40/#doors-menu) 2) Door operator power supply (MOT3 board for three-phase ports/AUTO board for regulated door operators) and fuses; 3) Door close contactors RFB (menu I/O PlayPad pagina 3, see https://dido.dmg.it/it/knowledge-base/controller-p40/#i-o-status-menu); 4) Set a different time (https://dido.dmg.it/it/knowledge-base/controller-p40/#doors-menu) | Door with limit switch (set https://dido.dmg.it/knowledge-base/controller-p40/#doors-menu) Door open limit switch FFB and door open contactors RFB status are viewable via Playpad in I/O status menu, Playboard in/out page 3 |
Fault 30 : The lift has been put out of service through external input (key switch on the hall station) and is parked at the preset floor. Turn the key back to “0” to put the lift back into service. | 30.0 | Out of service switch | Info | The lift has been put out of service through external input (key switch on the hall station) and is parked at the preset floor. Turn the key back to “0” to put the lift back into service. | The “Out-of-service” HS input on the controller has been activated. The lift goes to the predefined parking level and remains out of service until the command is deactivated. Changing the parking floor and the delay with which the controller activates the maneuver is also possible (https://dido.dmg.it/knowledge-base/controller-p40/#special-features-menu). | ||
Fault 30 : The lift has been put out of service through external input (key switch on the hall station) and is parked at the preset floor. Turn the key back to “0” to put the lift back into service. | 30.100 | Out of service switch | Info | The lift has been put out of service through external input (key switch on the hall station) and is parked at the preset floor. Turn the key back to “0” to put the lift back into service. | The “Out-of-service” IN2 input on the floor interface (BDU) has been activated. The lift goes to the predefined parking level and remains out of service until the command is deactivated. Changing the parking floor and the delay with which the controller activates the maneuver is also possible (https://dido.dmg.it/knowledge-base/controller-p40/#special-features-menu). | ||
Fault 30 : The lift has been put out of service through external input (key switch on the car station) and is parked at the preset floor. Turn the key back to “0” to put the lift back into service. | 30.200 | Out of service switch | Info | The lift has been put out of service through external input (key switch on the car station) and is parked at the preset floor. Turn the key back to “0” to put the lift back into service. | The SPARE input on the DMCPIT car interface behind the car operating panel has been activated. The lift goes to the predefined parking level and remains out of service until the command is deactivated. Changing the parking floor and the delay with which the controller activates the maneuver is also possible (https://dido.dmg.it/knowledge-base/controller-p40/#special-features-menu). | ||
Fault 31 : Simultaneous variation or wrong sequence of FAI/FAS positioning sensors | 31.0 | Counting error with magnetic sensor | Warning | Simultaneous variation or wrong sequence of FAI/FAS positioning sensors | The error could be caused by: 1) Incorrect positioning of the magnets in the shaft 2) Magnetic reader not fixed correctly (unstable) 3) Magnetization of the guide or fixings 4) Improper wiring of the readers The subcode precisely indicates the front of the magnet where the problem was detected (Front from 1 to 6 – see diagram). | Check: 1) Sensors and magnet position 2) Moving the sensor fixing 3) The wiring to the TOC board 4) The sensor with a multimeter. The contact must be closed in front of the magnet | Pos 0 is the absolute reference of the lowest floor |
Fault 32 : Impossible to move the car in “Temporary” mode if the main switch is not set to INSPECTION. | 32.0 | Temporary operation without inspection | Info | Impossible to move the car in “Temporary” mode if the main switch is not set to INSPECTION. | The system is in temporary operation. The switch on the controller is not set to “Inspection”. Thefault indicates that the system must switch to Inspection in order to move, i.e. the REV or REV1 or REV2 input must be active. If one of these three inputs is not active, the system remains stationary. | Check input REV, REV1 or REV2 (NC contacts). REV, REV1 and REV2 are viewable via PlayPad, Status I/O menu, Playboard I/O page 8 | |
Fault 33 : Inaccurate stop at floor. | 33.1 | Inaccurate stop | Warning | Inaccurate stop at floor. | The lift made an inaccurate stop at the floor, out of the limits set by RLS (“arrival distance to the floor UP”) and RLD (“arrival distance to the floor DOWN”) parameters. The RLS and RLD parameters are set automatically after the panel’s self-learning maneuver, and can be modified via a dedicated menu on the PlayPad | Check: 1) Position of the magnets (see wiring diagrams); 2) Slowing distances to the floor; 3) Check parameter C07 – Pull-in speed (minimum value set to 1/10th of the rated speed) on PlayPad / VVVF menu (https://dido.dmg.it/it/knowledge-base/controller-p40/#vvvf-menu); 4) The motor brakes. | |
Fault 33 : Inaccurate stop at floor. | 33.2 | Inaccurate stop | Warning | Inaccurate stop at floor. | The lift made an inaccurate stop at the floor, out of the limits set by RLS (“arrival distance to the floor UP”) and RLD (“arrival distance to the floor DOWN”) parameters. The RLS and RLD parameters are set automatically after the panel’s self-learning maneuver, and can be modified via a dedicated menu on the PlayPad | Check : 1) The “Stopping Boost” parameter on PlayPad / Counting menu (https://dido.dmg.it/it/knowledge-base/controller-p40/#system-positioning-menu), i.e., the approach speed of the system. This parameter should be set at 2% of the rated speed (VVVF closed loop) or 4% (VVVF open loop); 2) The motor brakes; 3) The arrival distances to the floor (parameters RLD and RLS). | |
Fault 33 : Inaccurate stop at floor. | 33.3 | Inaccurate stop | Warning | Inaccurate stop at floor. | The lift made an inaccurate stop at the floor, out of the limits set by RLS (“arrival distance to the floor UP”) and RLD (“arrival distance to the floor DOWN”) parameters. The RLS and RLD parameters are set automatically after the panel’s self-learning maneuver, and can be modified via a dedicated menu on the PlayPad | Check : 1) The “Stopping Boost” parameter on PlayPad / Counting menu (https://dido.dmg.it/it/knowledge-base/controller-p40/#system-positioning-menu), i.e., the approach speed of the system. This parameter should be set at 2% of the rated speed (VVVF closed loop) or 4% (VVVF open loop); 2) The motor brakes; 3) The arrival distances to the floor (parameters RLD and RLS). | |
Fault 33 : Inaccurate stop at floor. | 33.4 | Inaccurate stop | Warning | Inaccurate stop at floor. | The lift made an inaccurate stop at the floor, out of the limits set by RLS (“arrival distance to the floor UP”) and RLD (“arrival distance to the floor DOWN”) parameters. The RLS and RLD parameters are set automatically after the panel’s self-learning maneuver, and can be modified via a dedicated menu on the PlayPad | Check: 1) Position of the magnets (see wiring diagrams); 2) Slowing distances to the floor and stopping point; 3) The low speed setting (valve/electronic control unit parameter) 4) The valve circuit. | |
Fault 33 : Inaccurate stop at floor. | 33.5 | Inaccurate stop | Warning | Inaccurate stop at floor. | The lift made an inaccurate stop at the floor, out of the limits set by RLS (“arrival distance to the floor UP”) and RLD (“arrival distance to the floor DOWN”) parameters. The RLS and RLD parameters are set automatically after the panel’s self-learning maneuver, and can be modified via a dedicated menu on the PlayPad | Check: 1) Slowing distances to the floor; 2) The arrival distances to the floor (parameters RLD and RLS); 3) The low speed setting (valve/electronic control unit parameter) 4) The valve circuit. | |
Fault 33 : Inaccurate stop at floor. | 33.6 | Inaccurate stop | Warning | Inaccurate stop at floor. | The lift made an inaccurate stop at the floor, out of the limits set by RLS (“arrival distance to the floor UP”) and RLD (“arrival distance to the floor DOWN”) parameters. The RLS and RLD parameters are set automatically after the panel’s self-learning maneuver, and can be modified via a dedicated menu on the PlayPad | Check: 1) Slowing distances to the floor; 2) The arrival distances to the floor (parameters RLD and RLS); 3) The low speed setting (valve/electronic control unit parameter) 4) The valve circuit. | |
Fault 33 : Inaccurate stop at floor. | 33.0 | Inaccurate stop | Warning | Inaccurate stop at floor. | The lift made an inaccurate stop at the floor, out of the limits set by RLS (“arrival distance to the floor UP”) and RLD (“arrival distance to the floor DOWN”) parameters. The RLS and RLD parameters are set automatically after the panel’s self-learning maneuver, and can be modified via a dedicated menu on the PlayPad | Electric Controller In case of magnet and magnetic switch Check: 1) Position of the magnets (see wiring diagrams); 2) Slowing distances to the floor; 3) Check parameter C07 – Pull-in speed (minimum value set to 1/10th of the rated speed) on PlayPad / VVVF menu (https://dido.dmg.it/it/knowledge-base/controller-p40/#vvvf-menu); 4) The motor brakes. In case of DMG Rope Encoder or ELGO Check: 1) The “Stopping Boost” parameter on PlayPad / Counting menu (https://dido.dmg.it/it/knowledge-base/controller-p40/#system-positioning-menu), i.e., the approach speed of the system. This parameter should be set at 2% of the rated speed (VVVF closed loop) or 4% (VVVF open loop); 2) The motor brakes; 3) The arrival distances to the floor (parameters RLD and RLS). Hydraulic Controller In case of magnet and magnetic switch Check: 1) Position of the magnets (see wiring diagrams); 2) Slowing distances to the floor and stopping point; 3) The low speed setting (valve/electronic control unit parameter) 4) The valve circuit. In case of DMG Rope Encoder or ELGO Check: 1) Slowing distances to the floor; 2) The arrival distances to the floor (parameters RLD and RLS); 3) The low speed setting (valve/electronic control unit parameter) 4) The valve circuit. | |
Fault 34 : “Anti-nuisance” function activated: too many simultaneous calls from the lift car. Calls are canceled. | 34.0 | Anti-nuisance | Warning | “Anti-nuisance” function activated: too many simultaneous calls from the lift car. Calls are canceled. | (With the “anti-nuisance” function active) An excessive number of car calls have been activated without: – The photocell being interrupted (in the case of automatic doors); – The landing door having been opened (in other cases). Cabin calls are cancelled and the lift continues to be available | Change the number of unwanted calls in the Anti-nuisance parameter on PlayPad / Special Features / Anti-nuisance fault (https://dido.dmg.it/knowledge-base/controller-p40/#special-features-menu). | |
Fault 35 : The lift cannot serve calls and therefore is not considered for multiplex calls. | 35.100 | Lift not avalaible | Warning | The lift cannot serve calls. In the case of a multiplex system, is not considered for multiplex calls. | Photocell or door opener active for more than twice as long as the standby time with open doors (e.g. for people standing in front of photocells or door skids). In these cases the lift makes 3 attempts to start. If they fail, the lift is unavailable for floor calls for 1 min. | Check: 1) The presence of physical obstructions at the photocell; 2) Increase door closing time (https://dido.dmg.it/it/knowledge-base/controller-p40/#doors-menu) | |
Fault 35 : The lift cannot serve calls and therefore is not considered for multiplex calls. | 35.200 | Lift not avalaible | Warning | The lift cannot serve calls. In the case of a multiplex system, is not considered for multiplex calls. | No signal from the safety contact upstream of Point #4 (preliminary floor locks). The manual door may not be closed. In such cases the lift makes 3 attempts to start. If failed, the lift is unavailable for floor calls for 1 min. | Check: 1) Preliminary floor doors SD1-SD2; 2) The correct closing of the landing doors | |
Fault 35 : The lift is unavailable and cannot serve calls. | 35.10 | Lift not avalaible | Alert | The lift is unavailable and cannot serve calls. | Car light power failure or cabin light failure, for all types of systems. The system is stopped with open doors. The error is active if the LE input is active (can be checked via PlayPad diagnostics, I/O status menu page 1 https://dido.dmg.it/it/knowledge-base/controller-p40/#i-o-status-menu) | Check: 1) Presence of voltage on the power supply line; 2) Presence of light in the car. | |
Fault 36 : Wrong sequence in input phases. Could be detected even during system shutdown. | 36.0 | Phase sequence | Alert | Wrong sequence in input phases. Could be detected even during system shutdown. | Wrong sequence in input phases | Check the right sequence of phases or swap two phases on power input terminals L1-L2-L3. It is possible to check the input RPH status via PlayPad, I/O status menu, Playboard IN/OUT page 4 (https://dido.dmg.it/it/knowledge-base/controller-p40/#i-o-status-menu ). If the input is active, the phases are faulty | |
Fault 37 : Low charge on 24V battery. | 37.0 | Low battery | Warning | Low charge on 24V battery. | Possible causes of the fault: 1) Batteries disconnected or not functioning; 2) Batteries no longer capable of maintaining an adequate charge. This usually occurs four years after the first charge (the date of first charge is marked on the battery label); 3) Battery charger not working (CHAR board). | Check: 1) The status of the LEDs on the CHAR board (YELLOW: test in progress; GREEN: batteries OK; RED: low batteries or disconnected). The test can be forced by pushing the button next to the LED on the CHAR board. If the test fails with the batteries connected, check the batteries one by one; 2) The voltage of the batteries. The voltage value must be higher than 12V. Otherwise, replace the batteries; 3)Measure the voltage on the power cables of the batteries (disconnected). The voltage must be at least 27V. If lower, replace the char board or check the loads connected to the batteries. | |
Fault 38 : Safety chain point #0 is interrupted (during travel or while the lift is not moving). Landing calls and the elevator car movements are deleted On the PlayPad Led SE0 is off | 38.0 | Safety 0 open | Alert | Safety chain point #0 is interrupted (during travel or while the lift is not moving). Landing calls and the elevator car movements are deleted On the PlayPad Led SE0 is off | Safety 0 open during travel. DIS protection in Point #0 is open during travel. The car cannot move normally and calls are inhibited | Check: – The operation of the circuit breaker; – That the safety circuit is not grounded; – Any STOP close near the motor | |
Fault 38 : Safety chain point #1 is interrupted (during travel or while the lift is not moving). Landing calls and the elevator car movements are deleted On the PlayPad Led S1 is off | 38.1 | Safety 1 open | Alert | Safety chain point #1 is interrupted (during travel or while the lift is not moving). Landing calls and the elevator car movements are deleted On the PlayPad Led S1 is off | Safety 1 open during travel. A safety contact ahead of Point #1 (Shaft stop zone and PIT Inspection box) is open during travel. The car cannot move normally and calls are inhibited | Check all contacts between the terminals: SP3 and SP4 (STOP in the pit, pit ladder, Inspection box, etc.) | |
Fault 38 : Safety chain point #2 is interrupted (during travel or while the lift is not moving). Landing calls and the elevator car movements are deleted On the PlayPad Led SE2 is off | 38.2 | Safety 2 open | Alert | Safety chain point #2 is interrupted (during travel or while the lift is not moving). Landing calls and the elevator car movements are deleted On the PlayPad Led SE2 is off | Safety 2 open during travel. A safety contact ahead of Point #2 (Top of car stop and TOC Inspection box) is open during travel. The car cannot move normally and calls are inhibited | Check all contacts between the terminals: SC1 and SC2 (STOP on the Toc, Toc protection, Inspection box, etc) | |
Fault 39 : Ambient temperature too low! The car remains parked at the floor until the ambient temperature returns above the minimum threshold set. | 39.100 | Ambient temperature | Alert | Ambient temperature too low! The car remains parked at the floor until the ambient temperature returns above the minimum threshold set. | The ambient temperature detected by the sensor is lower than the minimum limit set (Threshold between -10°C and +5°C). | Check: 1) The presence of the temperature sensor; 2) The correctness of the sensor measurement; 3) The connection of the temperature sensor with the controller motherboard (input J18); 4) Activation, the threshold adjustment and sensor calibration in the PlayPad “Special Features menu” (see https://dido.dmg.it/knowledge-base/controller-p40/#special-features-menu) | |
Fault 39 : Ambient temperature too high! The car remains parked at the floor until the ambient temperature returns below the maximum threshold set. | 39.200 | Ambient temperature | Alert | Ambient temperature too high! The car remains parked at the floor until the ambient temperature returns below the maximum threshold set. | The ambient temperature detected by the sensor is higher than the maximum limit set (Threshold between +40°C and +75°C). | Check: 1) The presence of the temperature sensor; 2) The correctness of the sensor measurement; 3) The connection of the temperature sensor with the controller motherboard (input J18); 4) Activation, the threshold adjustment and sensor calibration in the PlayPad “Special Features menu” (see https://dido.dmg.it/knowledge-base/controller-p40/#special-features-menu) | |
Fault 40 : Pit access alarm (EN81-20 standard) | 40.20 | Access to Pit | Alert + Reset | Pit access alarm (EN81-20 standard) | The floor door on the lowest floor was opened to access the pit (manual unlocking of the floor door with monostable or bistable contacts). According to the EN81.20 code, this access causes the system to block and requires a specific reset procedure The same error can also be activated on systems without a landing door release contact, following: a) Activation of the STOP in the pit b) Activation of INSPECTION mode from the inspection box c) Opening the safety chain between points #1 and #0 (LED S1 off and S0 on on the PlayPad) d) Involuntary opening of the SE1 circuit (false contact, loose wire…) In all these cases, error 38 is also activated (subcode 1 – Point #1 open) | After resetting the STOP button in the pit/top of car and switching to “Normal mode”, perform the specific error reset in one of these ways: – Via specific menu on the Playpad (https://dido.dmg.it/knowledge-base/controller-p40/#faults-menu) – 3 consecutive activations of the landing door switch (where the double contact is present) – 3 consecutive activations of the down button on the inspection panel on the controller | |
Fault 40 : Pit access alarm (EN81-21 standard) | 40.21 | Access to Shaft | Alert + Reset | Pit access alarm (EN81-21 standard) | A floor door has been opened to access the pit or car roof (manual floor door release with monostable or bistable contacts). Because the system includes small spaces in the headroom and/or pit, according to EN81.21, this access is a reason for system lockout and requires a special reset procedure. | After resetting the STOP button in the pit/top of car and switching to “Normal mode”, perform the specific error reset in one of these ways: – Via specific menu on the Playpad (https://dido.dmg.it/knowledge-base/controller-p40/#faults-menu) – 3 consecutive activations of the landing door switch (where the double contact is present) – 3 consecutive activations of the down button on the inspection panel on the controller | |
Fault 40 : Monitor error RSDC relay (contact does not open) | 40.111 | Access to Shaft | Alert + Reset | Monitor error RSDC relay (contact does not open) | Problem monitoring relays inside the controller | Contact DMG technical support | |
Fault 40 : Bistable reset circuit (Automatic contact reset) | 40.121 | Access to Shaft | Alert + Reset | Bistable reset circuit (Automatic contact reset) | Problem monitoring relays inside the controller | Contact DMG technical support | |
Fault 40 : Error on the monostable circuit relating to the RSR1 relay | 40.131 | Access to Shaft | Alert + Reset | Error on the monostable circuit relating to the RSR1 relay | An opening of one or more safety contacts in the shaft has been detected without unlocking the access doors. Since the system has limited space in the headroom and/or pit, according to the EN81.21 standard the error is blocking and requires a specific reset procedure. The cause may be: a) Activation of the STOP in the pit b) Activation of the INSPECTION mode from the Inspection box in the pit c) Opening of the safety chain between points #1 and #0 (on the PlayPad LED S1 off and S0 on) d) Involuntary opening of the SE1 circuit (false contact, disconnected wire…) Note: together with this error, error 38 is also activated (subcode 1 – Point #1 open) | After resetting the STOP button in the pit/top of car and switching to “Normal mode”, perform the specific error reset in one of these ways: – Via specific menu on the Playpad (https://dido.dmg.it/knowledge-base/controller-p40/#faults-menu) – 3 consecutive activations of the landing door switch (where the double contact is present) – 3 consecutive activations of the down button on the inspection panel on the controller | |
Fault 40 : Error on the monostable circuit relating to the RSR2 relay | 40.132 | Access to Shaft | Alert + Reset | Error on the monostable circuit relating to the RSR2 relay | An opening of one or more safety contacts in the shaft has been detected without unlocking the access doors. Since the system has limited space in the headroom and/or pit, according to the EN81.21 standard the error is blocking and requires a specific reset procedure. The cause may be: a) Activation of the STOP in the pit b) Activation of the INSPECTION mode from the Inspection box in the pit c) Opening of the safety chain between points #1 and #0 (on the PlayPad LED S1 off and S0 on) d) Involuntary opening of the SE1 circuit (false contact, disconnected wire…) Note: together with this error, error 38 is also activated (subcode 1 – Point #1 open) | After resetting the STOP button in the pit/top of car and switching to “Normal mode”, perform the specific error reset in one of these ways: – Via specific menu on the Playpad (https://dido.dmg.it/knowledge-base/controller-p40/#faults-menu) – 3 consecutive activations of the landing door switch (where the double contact is present) – 3 consecutive activations of the down button on the inspection panel on the controller | |
Fault 41 : Monitoring fault for the R-ISO relay (safety circuit to monitor car movements with open doors). The lift is placed in “out of service” at the top floor (electric lift) or bottom floor (hydraulic lift). | 41.10 | Fault ISO | Alert + Reset | Monitoring fault for the R-ISO relay (safety circuit to monitor car movements with open doors). The lift is placed in “out of service” at the top floor (electric lift) or bottom floor (hydraulic lift). | Activation of the R-ISO relay monitor function relating to the safety circuit for re-levelling and/or early opening manoeuvres. | Check the alignment of ISO1 and ISO2. Reset ISO in the menu Faults | |
Fault 41 : The SM2 safety module monitoring (protection for open door manouvers) has detected an error while the cabin is NOT at floor. The lift is forcibly put into “out of service” at the top floor (electric lift) or bottom floor (hydraulic lift). | 41.10 | Fault ISO | Alert + Reset | The SM2 safety module monitoring (protection for open door manouvers) has detected an error while the cabin is NOT at floor. The lift is forcibly put into “out of service” at the top floor (electric lift) or bottom floor (hydraulic lift). | SM2 safety module monitor error with cabin not at floor | Check the alignment of ISO1 and ISO2. Reset ISO in the menu Faults | |
Fault 41 : The SM2 safety module monitoring (protection for open door manouvers) has detected an error while the cabin is at floor. The lift is forcibly put into “out of service” at the top floor (electric lift) or bottom floor (hydraulic lift). | 41.200 | Fault ISO | Alert + Reset | The SM2 safety module monitoring (protection for open door manouvers) has detected an error while the cabin is at floor. The lift is forcibly put into “out of service” at the top floor (electric lift) or bottom floor (hydraulic lift). | SM2 safety module monitor error with cabin at floor | Check the alignment of ISO1 and ISO2. Reset ISO in the menu Faults | |
Fault 42 : No serial link between controller and elevator car | 42.0 | TOC Communication | Alert | No serial link between controller and elevator car | 1) (Temporary)Loss of connection between the control panel and the lift car 2) Physical obstructions in connection cables 3) Electromagnetic disturbances 4) Protection against electrical leakage | Check: 1) CAN link between controller and top of elevator car board; 2) No interruptions in the connection cables; 3) The correct connection of the motor shielding; 4) Grounding wires. If the problem is not solved, disconnect all TOC board peripherals and reconnect them one by one to verify the source of the problem. | |
Fault 43 : The system is in Inspection mode (NORM/ISP switch set to Inspection). | 43.1 | Inspection | Info | The system is in Inspection mode (NORM/ISP switch set to Inspection). | REV input open (STD Version) | REV = PME REV1 = TOC REV2 = PIT Inspection |
|
Fault 43 : The system is in Inspection mode (NORM/ISP switch set to Inspection). | 43.2 | Inspection | Info | The system is in Inspection mode (NORM/ISP switch set to Inspection). | TOC’s REV1 input open | REV = PME REV1 = TOC REV2 = PIT Inspection |
|
Fault 43 : The system is in Inspection mode (NORM/ISP switch set to Inspection). | 43.3 | Inspection | Info | The system is in Inspection mode (NORM/ISP switch set to Inspection). | REV + TOC’s REV1 input open | REV = PME REV1 = TOC REV2 = PIT Inspection |
|
Fault 43 : The system is in Inspection mode (NORM/ISP switch set to Inspection). | 43.5 | Inspection | Info | The system is in Inspection mode (NORM/ISP switch set to Inspection). | REV input open (Pitagora version) | REV = PME REV1 = TOC REV2 = PIT Inspection |
|
Fault 43 : The system is in Inspection mode (NORM/ISP switch set to Inspection). | 43.6 | Inspection | Info | The system is in Inspection mode (NORM/ISP switch set to Inspection). | REV1 input open | REV = PME REV1 = TOC REV2 = PIT Inspection |
|
Fault 43 : The system is in Inspection mode (NORM/ISP switch set to Inspection). | 43.7 | Inspection | Info | The system is in Inspection mode (NORM/ISP switch set to Inspection). | REV + TOC’s REV1 input open | REV = PME REV1 = TOC REV2 = PIT Inspection |
|
Fault 43 : The system is in Inspection mode (NORM/ISP switch set to Inspection). | 43.11 | Inspection | Info | The system is in Inspection mode (NORM/ISP switch set to Inspection). | PME inspection (REV) | REV = PME REV1 = TOC REV2 = PIT Inspection |
|
Fault 43 : The system is in Inspection mode (NORM/ISP switch set to Inspection). | 43.12 | Inspection | Info | The system is in Inspection mode (NORM/ISP switch set to Inspection). | TOC inspection (REV1) | REV = PME REV1 = TOC REV2 = PIT Inspection |
|
Fault 43 : The system is in Inspection mode (NORM/ISP switch set to Inspection). | 43.13 | Inspection | Info | The system is in Inspection mode (NORM/ISP switch set to Inspection). | PME + TOC inspection (REV + REV1) | REV = PME REV1 = TOC REV2 = PIT Inspection |
|
Fault 43 : The system is in Inspection mode (NORM/ISP switch set to Inspection). | 43.14 | Inspection | Info | The system is in Inspection mode (NORM/ISP switch set to Inspection). | PIT Inspection (REV2) | REV = PME REV1 = TOC REV2 = PIT Inspection |
|
Fault 43 : The system is in Inspection mode (NORM/ISP switch set to Inspection). | 43.15 | Inspection | Info | The system is in Inspection mode (NORM/ISP switch set to Inspection). | PME + PIT Inspection (REV + REV2) | REV = PME REV1 = TOC REV2 = PIT Inspection |
|
Fault 43 : The system is in Inspection mode (NORM/ISP switch set to Inspection). | 43.16 | Inspection | Info | The system is in Inspection mode (NORM/ISP switch set to Inspection). | TOC + PIT Inspection (REV1 + REV2) | REV = PME REV1 = TOC REV2 = PIT Inspection |
|
Fault 43 : The system is in Inspection mode (NORM/ISP switch set to Inspection). | 43.17 | Inspection | Info | The system is in Inspection mode (NORM/ISP switch set to Inspection). | PME + TOC + PIT Inspection (REV + REV1 + REV2) | REV = PME REV1 = TOC REV2 = PIT Inspection |
|
Fault 44 : Re-levelling procedure not completed. All subsequent re-levelling requests at the same floor are inhibited. | 44.1 | Re-levelling not completed | Alert | Re-levelling procedure not completed. All subsequent re-levelling requests at the same floor are inhibited. | Re-levelling procedure was not completed within 10 seconds. | Check: 1) STOPPING BOOST parameter. Increase in steps of 0.5 through the dedicated menu on PlayPad (https://dido.dmg.it/knowledge-base/controller-p40/#system-positioning-menu); 2) ISO relay; 3) The SM2 module and/or its ZP1-ZP2 sensors (NO contacts); 4) Activation of contact SR2 (located on the car roof) and relative wiring. The activation status can also be consulted via PlayPad (https://dido.dmg.it/knowledge-base/controller-p40/#i-o-status-menu see ELGO input) | |
Fault 44 : Re-levelling procedure not completed. All subsequent re-levelling requests at the same floor are inhibited. | 44.2 | Re-levelling not completed | Alert | Re-levelling procedure not completed. All subsequent re-levelling requests at the same floor are inhibited. | Re-levelling procedure was not completed within 10 seconds. | Check: 1) STOPPING BOOST parameter. Increase in steps of 0.5 through dedicated menu on PlayPad (https://dido.dmg.it/knowledge-base/controller-p40/#system-positioning-menu); 2) ISO relay; 3) The SM2 module and/or its ZP1-ZP2 sensors (NO contacts); 4) ZP1 ENCODER and pulser; 5) Correct activation of module SM2 (located on the control panel). Correct activation can be seen by the simultaneous lighting of the four LEDs (S1, S2, OUT and POWER) on the SM2 module | |
Fault 44 : Re-levelling procedure not completed. All subsequent re-levelling requests at the same floor are inhibited. | 44.3 | Re-levelling not completed | Alert | Re-levelling procedure not completed. All subsequent re-levelling requests at the same floor are inhibited. | Re-levelling procedure was not completed within 10 seconds. | Check: 1) STOPPING BOOST parameter. Increase in steps of 0.5 through dedicated menu on PlayPad (https://dido.dmg.it/knowledge-base/controller-p40/#system-positioning-menu); 2) ISO relay; 3) The SM2 module and/or its ZP1-ZP2 sensors (NO contacts); 4) Magnet and magnetic switch counting system; 5) Correct activation of module SM2 (located on the control panel). Correct activation can be seen by the simultaneous lighting of the four LEDs (S1, S2, OUT and POWER) on the SM2 module | |
Fault 44 : Re-levelling procedure not completed. All subsequent re-levelling requests at the same floor are inhibited. | 44.4 | Re-levelling not completed | Alert | Re-levelling procedure not completed. All subsequent re-levelling requests at the same floor are inhibited. | Re-levelling procedure was not completed within 10 seconds. | Check: 1) Valve and motor activation circuit (refer to electrical drawing); 2) ISO relay; 3) The SM2 module and/or its ZP1-ZP2 sensors (NO contacts); 4) Activation of contact SR2 (located on the car roof) and relative wiring. The activation status can also be consulted via PlayPad (https://dido.dmg.it/knowledge-base/controller-p40/#i-o-status-menu see ELGO input) | |
Fault 44 : Re-levelling procedure not completed. All subsequent re-levelling requests at the same floor are inhibited. | 44.5 | Re-levelling not completed | Alert | Re-levelling procedure not completed. All subsequent re-levelling requests at the same floor are inhibited. | Re-levelling procedure was not completed within 10 seconds. | Check: 1) Valve and motor activation circuit (refer to electrical drawing); 2) ISO relay; 3) The SM2 module and/or its ZP1-ZP2 sensors (NO contacts); 4) ENCODER and ZP1 magnetic switch; 5) Correct activation of module SM2 (located on the control panel). Correct activation can be seen by the simultaneous lighting of the four LEDs (S1, S2, OUT and POWER) on the SM2 module | |
Fault 44 : Re-levelling procedure not completed. All subsequent re-levelling requests at the same floor are inhibited. | 44.6 | Re-levelling not completed | Alert | Re-levelling procedure not completed. All subsequent re-levelling requests at the same floor are inhibited. | Re-levelling procedure was not completed within 10 seconds. | Check: 1) Valve and motor activation circuit (refer to electrical drawing); 2) ISO relay; 3) The SM2 module and/or its ZP1-ZP2 sensors (NO contacts); 4) Magnet and magnetic switch counting system; 5) Correct activation of module SM2 (located on the control panel). Correct activation can be seen by the simultaneous lighting of the four LEDs (S1, S2, OUT and POWER) on the SM2 module | |
Fault 44 : Re-levelling procedure not completed. All subsequent re-levelling requests at the same floor are inhibited. | 44.0 | Re-levelling not completed | Alert | Re-levelling procedure not completed. All subsequent re-levelling requests at the same floor are inhibited. | Re-levelling procedure was not completed within 10 seconds. | Electric Controller In case of ELGO Check: 1) STOPPING BOOST parameter. Increase in steps of 0.5 through the dedicated menu on PlayPad (https://dido.dmg.it/knowledge-base/controller-p40/#system-positioning-menu); 2) ISO relay; 3) The SM2 module and/or its ZP1-ZP2 sensors (NO contacts); 4) Activation of contact SR2 (located on the car roof) and relative wiring. The activation status can also be consulted via PlayPad (https://dido.dmg.it/knowledge-base/controller-p40/#i-o-status-menu see ELGO input) In case of DMG Rope Encoder Check: 1) STOPPING BOOST parameter. Increase in steps of 0.5 through dedicated menu on PlayPad (https://dido.dmg.it/knowledge-base/controller-p40/#system-positioning-menu); 2) ISO relay; 3) The SM2 module and/or its ZP1-ZP2 sensors (NO contacts); 4) ZP1 ENCODER and pulser; 5) Correct activation of module SM2 (located on the control panel). Correct activation can be seen by the simultaneous lighting of the four LEDs (S1, S2, OUT and POWER) on the SM2 module In case of magnet and magnetic switch Hydraulic Controller In case of ELGO Check: 1) Valve and motor activation circuit (refer to electrical drawing); 2) ISO relay; 3) The SM2 module and/or its ZP1-ZP2 sensors (NO contacts); 4) Activation of contact SR2 (located on the car roof) and relative wiring. The activation status can also be consulted via PlayPad (https://dido.dmg.it/knowledge-base/controller-p40/#i-o-status-menu see ELGO input) In case of DMG Rope Encoder Check: 1) Valve and motor activation circuit (refer to electrical drawing); 2) ISO relay; 3) The SM2 module and/or its ZP1-ZP2 sensors (NO contacts); 4) ENCODER and ZP1 magnetic switch; 5) Correct activation of module SM2 (located on the control panel). Correct activation can be seen by the simultaneous lighting of the four LEDs (S1, S2, OUT and POWER) on the SM2 module In case of magnet and magnetic switch 1) Valve and motor activation circuit (refer to electrical drawing); 2) ISO relay; 3) The SM2 module and/or its ZP1-ZP2 sensors (NO contacts); 4) Magnet and magnetic switch counting system; 5) Correct activation of module SM2 (located on the control panel). Correct activation can be seen by the simultaneous lighting of the four LEDs (S1, S2, OUT and POWER) on the SM2 module | |
Fault 45 : The Door Zone (ZP) sensor did not detect the car’s entrance in the door zone. | 45.0 | Door Zone fault (ZP) | Warning | The Door Zone (ZP) sensor did not detect the car’s entrance in the door zone. | At floor, the ZP1 door zone contact stays open when the magnetic reader is in the door zone position. | Check the correct operation of the door zone sensor (if present); See Fault # 33. | |
Fault 46 : Indicates that the link between two or more controllers in the multiplex loop is missing. Every controller switch to SIMPLEX-like functioning | 46.0 | Multiplex link interrupted | Warning | Indicates that the link between two or more controllers in the multiplex loop is missing. Every controller switch to SIMPLEX-like functioning | The error could be caused by: 1) Wiring between cards; 2) Incorrect settings of the multiplex function; 3) Operating status of MTPX Line. | Check: 1) The connection between the controllers (MULX board). See https://dido.dmg.it/it/knowledge-base/multiplex-p40/; 2) All multiplex settings. See https://dido.dmg.it/knowledge-base/controller-p40/#configuration-menu; 3) The operating status via PlayPad, I/O Status Menu, MTPX Line (see https://dido.dmg.it/knowledge-base/controller-p40/#i-o-status-menu, Multiplex Line page). | |
Fault 46 : Indicates that the link between two or more controllers in the multiplex loop is missing. Every controller switch to SIMPLEX-like functioning | 46.255 | Multiplex link interrupted | Warning | Indicates that the link between two or more controllers in the multiplex loop is missing. Every controller switch to SIMPLEX-like functioning | Temporary restart of the micro dedicated to communication between Multiplex controllers | Check: 1) The connection between the controllers (MULX board). See https://dido.dmg.it/it/knowledge-base/multiplex-p40/; 2) Check the firmware version of the controller. If necessary, update it; 3) Contact DMG support. | |
Fault 47 : This fault indicates a problem within the error memory. | 47.0 | Memory Faults | Warning | This fault indicates a problem within the error memory. | Follow the procedure below: 1) Enter in Fault menu on the PlayPad; 2) Reset faults; 3) Verify that the error in question is no longer present in the PlayPad. | After this procedure, all the errors (even the inactive ones) will no longer be visible in the memory. | |
Fault 48 : Loss of connection between the controller and all BDU modules on the floors. | 48.0 | BDU link unavailable | Warning | Loss of connection between the controller and all BDU modules on the floors. | The BDU may be disconnected, unaddressed, or faulty. Check the LED status on each BDU: – GREEN LED flashing fast (0.5 sec): OK; – GREEN LED flashing fast (1 sec): BDU not addressed; – RED LED (fixed): BDU not working; – RED LED (flashing): no communication; – GREEN AND RED LED (flashing): communication synchronization in progress. | 1) Verify the correct physical connection between the various BDUs; 2) (slowly flashing green LED) Repeat the addressing procedure. To address the BDU, take the car to the floor and hold down any LOP button for 5 seconds; 3) (steady red LED) Try deleting and readdress the BDUs. To delete the BDU address, put the system in temporary mode and hold down the LOP button for the floor where the BDU is located for 10 seconds. Then address the BDU. To address the BDU, take the car to the floor and hold down any LOP button for 5 seconds. If the problem persists, replace the defective BDU. | You can check the floor where the BDU fault occuurred in “I/O Status” Menu on PlayPad. |
Fault 49 : Malfunctioning of one or more floor BDU interfaces. | 49.0 | BDU Fault | Warning | Malfunctioning of one or more floor BDU interfaces. | One or more BDUs may be broken or not working properly. The RED LED on the BDU is ON. | Try deleting and readdress the BDUs. To delete the BDU address, put the system in temporary mode and hold down the LOP button for the floor where the BDU is located for 10 seconds. Then address the BDU. To address the BDU, take the car to the floor and hold down any LOP button for 5 seconds. If the problem persists, replace the defective BDU (s). | You can check the floor where the BDU fault occurred in “I/O Status” Menu on PlayPad. |
Fault 50 : Activation of drift control function (if enabled). The lift is put out of service on an extreme floor. | 50.0 | Drift control | Alert + Reset | Activation of drift control function (if enabled). The lift is put out of service on an extreme floor. | Activation of anti-drifting function (norme NF P 82212) | If the system is equipped with it, this error indicates that the anti-drift function has been activated several times (5) in 2 minutes. According to the French standard NF P 82212, the lift is brought to safety at one of the extreme floors as a precaution. | 1) Check the effectiveness of the re-leveling and floor-leveling systems. 2) Reset error 82212 in the Errors menu |
Fault 51 : Wrong password for three times | 51.0 | Wrong Password | Warning | Wrong password for three times | Wrong Password | To unlock PlayPad features please contact DMG service | Lift continues to operate. You cannot access PlayPad features. |
Fault 52 : OC1 Code 1/2 – Overcurrent in acceleration | 52.xxx | Fault VVVF OC1 | Alert | OC1 Code 1/2 – Overcurrent in acceleration | During acceleration, an overcurrent was detected in the inverter and the short-circuit protection was activated. This error is tipically a consequence of ErE error (wrong pulse/RPM/frequency parameters) | 1) Check the correct opening of the brakes 2) Check if the power of the inverter matches the traction machine data 3) Verify the correct balancing of the lift 4) (Geared drive) Check if the motor tuning procedure was successfully completed 5) Check if the correct isolation of the traction machine | Repat the motor tuning procedure (VVVF Lift Setting – https://dido.dmg.it/it/knowledge-base/controller-p40/#vvvf-frenic-lift-setting) if needed |
Fault 52 : OC2 Code 3/4 – Overcurrent in deceleration | 52.xxx | Fault VVVF OC2 | Alert | OC2 Code 3/4 – Overcurrent in deceleration | During deceleration, an overcurrent was detected in the inverter and the short-circuit protection was activated. This error is tipically a consequence of ErE error (wrong pulse/RPM/frequency parameters) | 1) Check the correct opening of the brakes 2) Check if the power of the inverter matches the traction machine data 3) Verify the correct balancing of the lift 4) (Geared drive) Check if the motor tuning procedure was successfully completed 5) Check if the correct isolation of the traction machine | Repat the motor tuning procedure (VVVF Lift Setting – https://dido.dmg.it/it/knowledge-base/controller-p40/#vvvf-frenic-lift-setting) if needed |
Fault 52 : OC3 – Overcurrent during travel | 52.xxx | Fault VVVF OC3 | Alert | OC3 – Overcurrent during travel | At constant speed, an overcurrent was detected in the inverter and the ground fault protection was activated. This error is tipically a consequence of ErE error (wrong pulse/RPM/frequency parameters) | 1) Check the correct opening of the brakes 2) Check if the power of the inverter matches the traction machine data 3) Verify the correct balancing of the lift 4) (Geared drive) Check if the motor tuning procedure was successfully completed 5) Check if the correct isolation of the traction machine | Repat the motor tuning procedure (VVVF Lift Setting – https://dido.dmg.it/it/knowledge-base/controller-p40/#vvvf-frenic-lift-setting) if needed |
Fault 52 : Motor overload | 52.40 | Fault VVVF OL1 | Alert | Motor overload | The inverter detected an overload in the motor and the thermal protection was activated. This is possibly due to a blocked motor, cabin or counterweight or to the insufficient size of the inverter. | 1) Check if the motor, car or counterweight are blocked 2) Check if the power/current of the inverter matches the traction machine data 3) Check the correct opening of the brakes. 4) Check the values of parameters F10 to F12 | |
Fault 52 : Er7 Code 19 – Generic failure during pole tuning procedure. | 52.106 | Fault VVVF Er7 | Alert | Er7 Code 19 – Generic failure during pole tuning procedure. | The inverter detected an error during the motor tuning/pole tuning procedure: the values of relevant parameters are abnormal. This is possibly due to mismatch between the type encoder board (for gearless drive: EnDat / SinCos) and the value of the Parameter L01 (“PG select”) | 1 – Verify if Parameter L01 in the VVVF Menu matches the type of encoder applied to the machine 2 – Repeat the motor tuning procedure (VVVF Lift Setting – https://dido.dmg.it/it/knowledge-base/controller-p40/#vvvf-frenic-lift-setting) | Il link deve puntare a DIDO / VVVF Link setting |
Fault 52 : Er7 Code 21 – I/O failure during pole tuning procedure | 52.107 | Fault VVVF Er7 | Alert | Er7 Code 21 – I/O failure during pole tuning procedure | The inverter detected a I/O error during the motor tuning/pole tuning procedure. This is possibly due to the removal of the RUN command before the end of the tuning procedure or the interruption of the enable input. | Repeat the motor tuning procedure (VVVF Lift Setting – https://dido.dmg.it/it/knowledge-base/controller-p40/#vvvf-frenic-lift-setting) | Da aggiornare software per la visualizzazione dell’errore |
Fault 52 : Er7 Code 24 – Enable command failure | 52.108 | Fault VVVF Er7 | Alert | Er7 Code 24 – Enable command failure | The inverter detected the interruption of the Enable command during the motor tuning/pole tuning procedure. The ENABLE command and the DIRBRK command may be too close. | 1 – Increase the delay of Dir_BRK command in the System Positioning Menu – https://dido.dmg.it/it/knowledge-base/controller-p40/#system-positioning-menu 2 – Repeat the motor tuning procedure (VVVF Lift Setting – https://dido.dmg.it/it/knowledge-base/controller-p40/#vvvf-frenic-lift-setting) | |
Fault 52 : Er7 Code 52 – Failure during magnetic pole position offset tuning. Inconsistent results. | 52.113 | Fault VVVF Er7 | Alert | Er7 Code 52 – Failure during magnetic pole position offset tuning. Inconsistent results. | The inverter detected an inconsistent offset value in pole positions during the pole tuning procedure. | Verify the value of parameters and repeat the motor tuning procedure (VVVF Lift Setting – https://dido.dmg.it/it/knowledge-base/controller-p40/#vvvf-frenic-lift-setting) | |
Fault 52 : Overspeed error | 52.128 | Fault VVVF OS | Alert | Overspeed error | The inverter detected an overspeed and the protection was activated | 1) Check the encoder resolution setting in Parameter L02 2) Check the values for parameters F03, P01, L32 | Da aggiornare software per la visualizzazione dell’errore |
Fault 52 : Pg Code 61 – Serial encoder response timed out | 52.138 | Fault VVVF Pg | Alert | Pg Code 61 – Serial encoder response timed out | The encoder cable is broken or disconnected. | Check the wiring of the encoder | |
Fault 52 : Pg Code 71 – Serial encoder alarm | 52.142 | Fault VVVF Pg | Alert | Pg Code 71 – Serial encoder alarm | The encoder cable is broken or disconnected. | Check the wiring of the encoder | Da aggiornare software per la visualizzazione dell’errore |
Fault 52 : ErE Code 1 – MIsmatch between actual and expected pulses from the motor encoder | 52.146 | Fault VVVF ErE | Alert | ErE Code 1 – MIsmatch between actual and expected pulses from the motor encoder | Wrong setting in pulses, RPM, frequency (L02; F03; F04); | 1) Verify the values of Parameters L02-F03-F04 2) Geared: change Parameter H190 from 1 to 0 (invert phase) 3) Gearless: change Parameter H190 from 1 to 0 + repeat pole tuning 4) Check motor brake / car / counterweight blockage 5) Verify gains parameter (L38) 6) Check the mechanical fixing of the encoder | Da aggiornare software per la visualizzazione dell’errore |
Fault 52 : ErE Code 5 – Zero speed detected from encoder | 52.148 | Fault VVVF ErE | Alert | ErE Code 5 – Zero speed detected from encoder | Wrong setting in pulses, RPM, frequency (L02; F03; F04); | 1) Verify the values of Parameters L02-F03-F04 2) Geared: change Parameter H190 from 1 to 0 (invert phase) 3) Gearless: change Parameter H190 from 1 to 0 + repeat pole tuning 4) Check motor brake / car / counterweight blockage 5) Verify gains parameter (L38) 6) Check the mechanical fixing of the encoder | Da aggiornare software per la visualizzazione dell’errore |
Fault 52 : OLU Code 10 – Inverter Overload | 52.156 | Fault VVVF OLU | Alert | OLU Code 10 – Inverter Overload | The inverter detected an internal overload resulting in excessive temperature. At motor start, this error is tipically a consequence of ErE error (wrong pulse/RPM/frequency parameters). Alternatively, other possible causes are: – Over temperature in the IGBT – Failure of the cooling system – Switching frequency too high – Overload in the cabin | 1) See resolution steps of Error 52.146 (ErE VVVF error) 2) Check the cooling system 3) Verify the parameter F26 (Motor Sound) 4) Verify the cabin load | Da aggiornare software per la visualizzazione dell’errore |
Fault 53 : An open-door maneuver has been set but the lift does not have a UCMP solution. The cabin cannot move and a specific reset is required. | 53.1 | MIssing UCMP device | Alert + Reset | An open-door maneuver has been set but the lift does not have a UCMP solution. The cabin cannot move and a specific reset is required. | Open door operations (re-leveling or advance door opening) is not possible for 81-20 lifts without UCMP. | Check the “Releveling” parameter in the “Configuration” Menu and the “Advance Opening” parameter in the “Doors” Menu: both must be set to NO. Perform the specific error reset in the “Errors” Menu | |
Fault 53 : One or both engine brake elements are open while the car is stationary. The system remains blocked and does not accept calls. | 53.2 | Brake contact open | Alert + Reset | One or both engine brake elements are open while the car is stationary. The system remains blocked and does not accept calls. | At least one brake contact is open. Possible causes are: – Mechanical brake failure – Brake control electrical circuit failure – Brake position sensors faulty or incorrectly adjusted | Check – Correct brake operation – Brake-related position sensor | |
Fault 53 : One or both engine brake elements are closed while the car is moving. The system remains blocked and does not accept calls. | 53.3 | Brake contact closed | Alert + Reset | One or both engine brake elements are closed while the car is moving. The system remains blocked and does not accept calls. | At least one brake contact is close. Possible causes are: – Mechanical brake failure – Brake control electrical circuit failure – Brake position sensors faulty or incorrectly adjusted | Check – Correct brake operation – Brake-related position sensor | |
Fault 53 : Monitoring error on GMV NGV A3 power unit | 53.4 | Fault UCM on hydro unit | Alert + Reset | Monitoring error on GMV NGV A3 power unit | The outputs RDY and RUN are both OFF. Status visible from PlayPad | See the troubleshooting section for the GMV control unit | |
Fault 53 : Monitoring error on GMV NGV A3 power unit | 53.5 | Fault UCM on hydro unit | Alert + Reset | Monitoring error on GMV NGV A3 power unit | The outputs RDY and RUN are both ON. Status visible from PlayPad | See the troubleshooting section for the GMV control unit | |
Fault 53 : Monitoring error on hydro power unit with dual descent valve | 53.6 | Fault UCM on hydro unit | Alert + Reset | Monitoring error on hydro power unit with dual descent valve | One or both valves have not closed correctly or not completely – Leakage on the valve – Impurities in the valve – Electrical fault in the valve control circuit | Check – The Correct functioning of the valves – The electrical valve control circuit | The test consists in the separate activation of the two descent valves when the car is stopped at floor. In case of unexpecteded car movement (i.e.: oil leakage), the error is activated. |
Fault 53 : Monitoring error on START ELEVATOR ECUs power unit with dual descent valve | 53.8 | Fault UCM on hydro unit | Alert + Reset | Monitoring error on START ELEVATOR ECUs power unit with dual descent valve | One or both valves have not closed correctly or not completely – Leakage on the valve – Impurities in the valve – Electrical fault in the valve control circuit | Check – The Correct functioning of the valves – The electrical valve control circuit | The test consists in the separate activation of the two descent valves when the car is stopped at floor. In case of unexpecteded car movement (i.e.: oil leakage), the error is activated. |
Fault 53 : Monitoring error on BUCHER HYDRAULICS i-Valve power unit (SMA not at 0V) | 53.10 | Fault UCM on hydro unit | Alert + Reset | Monitoring error on BUCHER HYDRAULICS i-Valve power unit (SMA not at 0V) | SMA output is not activated as expected. Status visible from the PlayPad | See the troubleshooting section for the Bucher Hydraulics control unit | |
Fault 53 : Monitoring error on BUCHER HYDRAULICS i-Valve power unit (SMA not at 24V) | 53.11 | Fault UCM on hydro unit | Alert + Reset | Monitoring error on BUCHER HYDRAULICS i-Valve power unit (SMA not at 24V) | SMA output is not activated as expected. Status visible from the PlayPad | See the troubleshooting section for the Bucher Hydraulics control unit | |
Fault 53 : Problem with the Y2 valve of the START Elev. control unit while in motion | 53.12 | Fault UCM on hydro unit | Alert + Reset | Problem with the Y2 valve of the START Elev. control unit while in motion | Y2 monitor during travel | Check wiring and valve Y2 and its monitor signal | |
Fault 53 : Problem with the Y2 valve of the START Elev. control unit while the car is stopped | 53.13 | Fault UCM on hydro unit | Alert + Reset | Problem with the Y2 valve of the START Elev. control unit while the car is stopped | Y2 monitor with stationary car | Check wiring and valve Y2 and its monitor signal | |
Fault 53 : Problem with the Y3 valve of the START Elev. control unit while in motion | 53.14 | Fault UCM on hydro unit | Alert + Reset | Problem with the Y3 valve of the START Elev. control unit while in motion | Y3 monitor during travel | Check wiring and valve Y3 and its monitor signal | |
Fault 53 : Problem with the Y3 valve of the START Elev. control unit while the car is stopped | 53.15 | Fault UCM on hydro unit | Alert + Reset | Problem with the Y3 valve of the START Elev. control unit while the car is stopped | Y3 monitor with stationary car | Check wiring and valve Y3 and its monitor signal | |
Fault 53 : Activation of the UCM protection system due to a sudden movement of the cabin away from the floor. | 53.100 | Fault UCM | Alert + Reset | Activation of the UCM protection system due to a sudden movement of the cabin away from the floor. | An uncontrolled cabin movement occurred and the UCM protection circuit was activated | In case Fault 41 is also present (Fault ISO), check the sensors ZP1 and ZP2. | |
Fault 53 : A problem was detected on the RUCM1/RUCM2 relay monitoring circuit in the controller | 53.200 | Fault UCM | Alert + Reset | A problem was detected on the RUCM1/RUCM2 relay monitoring circuit in the controller | RUCM1/RUCM2 relay monitor error (contact does not open) | ||
Fault 53 : A problem was detected on the RUCM1 relay monitoring circuit in the controller | 53.201 | Fault UCM | Alert + Reset | A problem was detected on the RUCM1 relay monitoring circuit in the controller | RUCM1 relay monitor error (contact does not close) | ||
Fault 53 : A problem was detected on the RUCM2 relay monitoring circuit in the controller | 53.202 | Fault UCM | Alert + Reset | A problem was detected on the RUCM2 relay monitoring circuit in the controller | RUCM2 relay monitor error (contact does not close) | ||
Fault 53 : A problem was detected on the RUCM3 relay monitoring circuit in the controller | 53.203 | Fault UCM | Alert + Reset | A problem was detected on the RUCM3 relay monitoring circuit in the controller | RUCM3 relay monitor error (contact does not close) | ||
Fault 53 : The monitoring circuit of the A3 overspeed governor has detected the pin locked in the extended position | 53.204 | Locked pin on A3 speed limiter | Alert + Reset | The monitoring circuit of the A3 overspeed governor has detected the pin locked in the extended position | Monitor OSG A3 (stud stucked in extended position) | ||
Fault 53 : A problem was detected on the RUCM1 relay monitoring circuit in the panel. | 53.210 | Fault UCM | Alert + Reset | A problem was detected on the RUCM1 relay monitoring circuit in the panel. | RUCM1 Stucked Close | ||
Fault 53 : A problem was detected on the RUCM3 relay monitoring circuit in the panel. | 53.220 | Fault UCM | Alert + Reset | A problem was detected on the RUCM3 relay monitoring circuit in the panel. | RUCM2 Stucked Close | ||
Fault 53 : A problem was detected on the RUCM3 relay monitoring circuit in the panel. | 53.230 | Fault UCM | Alert + Reset | A problem was detected on the RUCM3 relay monitoring circuit in the panel. | RUCM3 Stucked Close | ||
Fault 53 : The monitoring circuit of the A3 overspeed governor has detected the pin locked in the retracted position | 53.240 | Fault UCM | Alert + Reset | The monitoring circuit of the A3 overspeed governor has detected the pin locked in the retracted position | Monitor OSG A3 (stud stucked in retracted position) | ||
Fault 54 : Safety edges activated. | 54.0 | Safety edges | Alert | Safety edges activated. | Safety edges activated during travel. The system is waiting for a new car call to resume operation. | Remove obstacles from the beams of the safety edges. | |
Fault 54 : Safety edge monitoring fault | 54.1 | Safety edges | Alert | Safety edge monitoring fault | CEDES safety edge test failed door side A | Check the photocell monitoring circuit | |
Fault 54 : Safety edge monitoring fault | 54.2 | Safety edges | Alert | Safety edge monitoring fault | CEDES safety edge test failed door side B | Check the photocell monitoring circuit | |
Fault 54 : Safety edge monitoring fault | 54.10 | Safety edges | Alert | Safety edge monitoring fault | KSA safety edge test failed | Check the photocell monitoring circuit | |
Fault 54 : Safety edge monitoring fault | 54.20 | Safety edges | Alert | Safety edge monitoring fault | KSB safety edge test failed | Check the photocell monitoring circuit | |
Fault 55 : Error on second contact door A | 55.2 | Door Contact Monitor (SCS) | Alert + Reset | Error on second contact door A | The safety chain monitoring has detected the opening of the second contact of door A (FFA input for door operators, CEA input for manual doors in the cabin) | Check the second contact of door A | |
Fault 55 : A jumper was detected on the safety contact of floor door A (point #4 of the safety chain) | 55.4 | Door Contact Monitor (SCS) | Alert + Reset | A jumper was detected on the safety contact of floor door A (point #4 of the safety chain) | The safety chain monitoring detected the presence of a jumper on the safety contact of floor door A and opened point SE4 of the safety chain | Check the floor door A safety contact (chain point #4 input) | |
Fault 55 : A jumper was detected on the safety contact of car door A (point #6 of the safety chain) | 55.6 | Door Contact Monitor (SCS) | Alert + Reset | A jumper was detected on the safety contact of car door A (point #6 of the safety chain) | The safety chain monitoring detected the presence of a jumper on the safety contact of car door A and opened point SE6 of the safety chain | Check car door A safety contact (chain point #6 input) | |
Fault 55 : Error on second contact door B | 55.12 | Door Contact Monitor (SCS) | Alert + Reset | Error on second contact door B | Safety chain monitoring has detected the opening of the second contact of door B (FFB input for door operators, CEB input for manual doors in the cabin) | Check the second contact of door B | |
Fault 55 : A jumper was detected on the safety contact of floor door B (point #4 of the safety chain) | 55.14 | Door Contact Monitor (SCS) | Alert + Reset | A jumper was detected on the safety contact of floor door B (point #4 of the safety chain) | The safety chain monitoring detected the presence of a jumper on the safety contact of floor door B and opened point SE4 of the safety chain | Check the floor door B safety contact (chain point #4 input) | |
Fault 55 : A jumper was detected on the safety contact of car door B (point #6 of the safety chain) | 55.16 | Door Contact Monitor (SCS) | Alert + Reset | A jumper was detected on the safety contact of car door B (point #6 of the safety chain) | The safety chain monitoring detected the presence of a jumper on the safety contact of car door B and opened point SE6 of the safety chain | Check car door B safety contact (chain point #6 input) | |
Fault 55 : After activating the door bypass, the SE6 contact did not close | 55.100 | Door Contact Monitor (SCS) | Alert + Reset | After activating the door bypass, the SE6 contact did not close | SE6 signal failure during bypass circuit activation | Check doors bypass Circuit (SE3-SC5) | |
Fault 56 : Involuntary access to the shaft through a manual door detected while the cabin is stopped off-level or on a different floor than the one with the door unlocked | 56.1 | Unintended Shaft Access | Alert + Reset | Involuntary access to the shaft through a manual door detected while the cabin is stopped off-level or on a different floor than the one with the door unlocked | UAS error is enabled only through the “Shaft protection” parameter of the “Special functions” Menu. A BDU with an additional door input must be used (can be NO or NC). The system detects the opening of a manual landing door by monitoring the auxiliary door input. | Reset UAS in the menu Faults (https://dido.dmg.it/it/knowledge-base/controller-p40/#faults-menu) | |
Fault 56 : Detected multiple manual landing doors open while the car is stopped off-floor or at a different floor than the one with the doors unlocked | 56.2 | Unintended Shaft Access | Alert + Reset | Detected multiple manual landing doors open while the car is stopped off-floor or at a different floor than the one with the doors unlocked | More than one Floor door manually open (at different floors) | Reset UAS in the menu Faults (https://dido.dmg.it/it/knowledge-base/controller-p40/#faults-menu) | |
Fault 57 : Bypass active on door safety contacts. The lift can be moved only in Inspection mode. | 57.1 | Bypass door | Info | Bypass active on door safety contacts. The lift can be moved only in Inspection mode. | The manual bypass command of the safety contacts ahead of Point #6 (car doors or reduced pit/headroom protection devices) has been activated. | ||
Fault 57 : Bypass active on door safety contacts. The lift can be moved only in Inspection mode. | 57.2 | Bypass door | Info | Bypass active on door safety contacts. The lift can be moved only in Inspection mode. | The manual bypass command of the safety contacts ahead of Point #4 (Floor preliminary locks) has been activated | ||
Fault 57 : Bypass active on door safety contacts. The lift can be moved only in Inspection mode. | 57.3 | Bypass door | Info | Bypass active on door safety contacts. The lift can be moved only in Inspection mode. | The manual bypass command of the safety contacts ahead of Point #5 (Floor doors) has been activated | ||
Fault 57 : Conflict between inspection modes from the controller and from the top of car/shaft box. | 57.100 | Inspection mode conflict | Alert | Conflict between inspection modes from the controller and from the top of car/shaft box. | The monitoring circuit of the SM1 safety module, dedicated to the bypass of the electric control panel (PME) in the controller, is open. The up/down buttons on the PME are not active and the manual movement of the cabin in inspection mode from the shaft control panels is prevented. The SE3 LED on the PlayPad is on. | Verify the correct functioning of the SM1 safety module. To restore correct operation, first set the PME selector to NORMAL and then back to INSPECTION. Check that the SE3 LED on the PlayPad turns off. | |
Fault 58 : Excessive car speed | 58.0 | Overspeed | Warning | Excessive car speed | In inspection or temporary mode, the lift car exceeds a speed of 0.63 m/s. The lift stops its travel. | To resume car movement – Release all travel controls; – Press the desired run command (up or down). If the error occurs again, check the encoder parameters or the inspection speed in “System Positioning” menu (https://dido.dmg.it/knowledge-base/controller-p40/#system-positioning-menu). The inspection speed must not exceed 0.63 m/s. | |
Fault 59 : Error in the retaining pin command of the pre-activated protection device. | 59.0 | 81.21 Device fault | Alert | Error in the retaining pin command of the pre-activated protection device. | The monitoring circuit of the pre-activated protection device for reduced spaces is faulty while the device is not powered. | Check the correct operation of the pre-activated device (or RMPP relay) | |
Fault 59 : Error on manual protection device 81-21 | 59.101 | 81.21 Device fault | Alert | Error on manual protection device 81-21 | Monitor Relay RMPP (contact doesn’t open), only for manual protection | Check the correct operation of the manual device (or RMPP relay) | |
Fault 59 : Error on manual protection device 81-21 | 59.102 | 81.21 Device fault | Alert | Error on manual protection device 81-21 | Monitor Relay RMPP (contact doesn’t close), only for manual protection | Check the correct operation of the manual device (or RMPP relay) | |
Fault 59 : Error in the retaining pin command of the pre-activated protection device. | 59.255 | 81.21 Device fault | Alert | Error in the retaining pin command of the pre-activated protection device. | Wrong feedback when pre-triggered device is energized | Check the correct operation of the pre-activated device (or RMPP relay) | |
Fault 60 : Cabin beyond upper limit | 60.0 | ELGO – Overtravel | Alert | Cabin beyond upper limit | The positioning system (ELGO Encoder) detected that the upper limit has been passed and stopped the cabin | Move the cabin down below the upper limit position and perform a specific reset for Error SE3 | |
Fault 60 : Cabin beyond lower limit | 60.1 | ELGO – Overtravel | Alert | Cabin beyond lower limit | The positioning system (ELGO Encoder) detected that the lower limit has been passed and stopped the cabin | Move the cabin up above the lower limit position and perform a specific reset for Error SE3 | |
Fault 60 : Upper inspection limit reached | 60.4 | ELGO – Inspection limits | Info | Upper inspection limit reached | The positioning system (ELGO Encoder) detected that the system has reached the inspection upper limit switch | ||
Fault 60 : Lower inspection limit reached | 60.5 | ELGO – Inspection limits | Info | Lower inspection limit reached | The positioning system (ELGO Encoder) detected that the system has reached the inspection lower limit switch | ||
Fault 60 : Excessive speed during normal mode (pre tripping) | 60.8 | Overspeed in normal mode | Alert | Excessive speed during normal mode (pre tripping) | The positioning system (ELGO Encoder) has detected that the cabin’s nominal speed has been exceeded and has blocked the cabin for a few seconds (pre-tripping). The reset is automatic. | 1) Check the nominal speed in normal mode 2) Check the ELGO’s configuration | |
Fault 60 : Excessive speed during normal mode (final tripping) | 60.9 | Overspeed in normal mode | Alert | Excessive speed during normal mode (final tripping) | The positioning system (ELGO Encoder) has detected that the cabin’s nominal speed has been exceeded and has blocked the cabin for a few seconds (final tripping). | 1) Check the nominal speed in normal mode 2) Check the ELGO’s configuration 3 )Perform a Fault reset | |
Fault 60 : Excessive speed during inspection mode (final tripping) | 60.11 | Overspeed in inspection mode | Alert | Excessive speed during inspection mode (final tripping) | The positioning system (ELGO Encoder) has detected that the lift nominal speed has been exceeded and has blocked the cabin for a few seconds (final tripping). | 1) Check the nominal speed in inspection mode 2) Check the ELGO’s configuration 3) Perform a Fault reset | |
Fault 60 : Excessive speed during teach mode (final tripping) | 60.13 | Overspeed in teach mode | Alert | Excessive speed during teach mode (final tripping) | The positioning system (ELGO Encoder) has detected that the lift nominal speed has been exceeded and has blocked the cabin for a few seconds (final tripping). | 1) Check the lift speed. Reduce it in Teach mode (max 0,6 m/s) 2) Check the ELGO’s configuration 3) Perform a Fault reset | |
Fault 60 : Excessive speed while approaching the floor | 60.14 | Overspeed in approaching floor | Warning | Excessive speed while approaching the floor | The positioning system (ELGO Encoder) has detected that the leveling limit speed (0.8m/s) during the stop at floor has been exceeded and has blocked the cabin for a few seconds. The reset is automatic. | 1) Check that the leveling speed set on the control unit does not exceed 0.8 m/s | |
Fault 60 : Excessive speed during re-leveling maneuver | 60.15 | Overspeed in releveling | Warning | Excessive speed during re-leveling maneuver | The positioning system (ELGO Encoder) has detected that the releveling limit speed (0.3m/s) has been exceeded and has blocked the cabin for a few seconds. The reset is automatic. The error may appear in hydraulic systems with hydraulic circuit sealing problems. | 1) Check that the re-leveling speed set on the control unit does not exceed 0.3 m/s 2) Check the tightness of the hydraulic circuit (piston) and the presence of air in the circuit | |
Fault 60 : Excessive speed during deceleration at the extreme limits | 60.16 | Overspeed in deceleration | Warning | Excessive speed during deceleration at the extreme limits | The positioning system (ELGO Encoder) has detected excessive speed during deceleration near extreme floors and has blocked the cabin. Reset is automatic. The error may appear in traction lifts with a deceleration curve not adequate for the deceleration distance. | Increase deceleration distance (R1D/R1S) | |
Fault 60 : ELGO Fault | 60.24 | Fault ELGO | Alert | ELGO Fault | Unintended car movement | ||
Fault 60 : ELGO not in operating mode | 60.100 | Fault ELGO | Alert | ELGO not in operating mode | The positioning system (ELGO Encoder) is not in operating mode and the cabin is blocked | The ELGO manual teach procedure is required to reset the system | |
Fault 60 : Fault of EN81-21 input in Manual Teach mode | 60.102 | ELGO – Manual Teach mode | Alert | Fault of EN81-21 input in Manual Teach mode | The positioning system (ELGO encoder) has detected that the EN81-21 input in manual teach-in mode is not functioning correctly | Check wiring of ZP2 signal in the controller | |
Fault 60 : eSGC_POW missing in Manual Teach mode | 60.103 | ELGO – Manual Teach mode | Alert | eSGC_POW missing in Manual Teach mode | The positioning system (ELGO encoder) detected that ELGO’s eSGC_POW is missing in manual teach-in mode | Check wiring of cable eSGC (power missing) | |
Fault 60 : ELGO restarts in Manual Teach mode | 60.104 | ELGO – Manual Teach mode | Alert | ELGO restarts in Manual Teach mode | The ELGO device is not functioning correctly | The ELGO device must be substituted | |
Fault 60 : ELGO input 81.21 not matching (always OFF) | 60.121 | ELGO Input mismatch | Alert | ELGO input 81.21 not matching (always OFF) | Mismatch between commands from controller and the ELGO encoder diagnostics was detected | 1) Check wiring of ELGO 2) Check TOC signal outputs | |
Fault 60 : ELGO UP/DOWN inputs not active | 60.122 | ELGO Input mismatch | Alert | ELGO UP/DOWN inputs not active | Mismatch between commands from controller and the ELGO encoder diagnostics was detected | 1) Check wiring of ELGO 2) Check TOC signal outputs | |
Fault 60 : ELGO UP input not matching | 60.123 | ELGO Input mismatch | Alert | ELGO UP input not matching | Mismatch between commands from controller and the ELGO encoder diagnostics was detected | 1) Check wiring of ELGO 2) Check TOC signal outputs | |
Fault 60 : ELGO DOWN input not matching | 60.124 | ELGO Input mismatch | Alert | ELGO DOWN input not matching | Mismatch between commands from controller and the ELGO encoder diagnostics was detected | 1) Check wiring of ELGO 2) Check TOC signal outputs | |
Fault 60 : ELGO UP/DOWN inputs not matching (always ON) | 60.125 | ELGO Input mismatch | Alert | ELGO UP/DOWN inputs not matching (always ON) | Mismatch between commands from controller and the ELGO encoder diagnostics was detected | 1) Check wiring of ELGO 2) Check TOC signal outputs | |
Fault 60 : Communication time out | 60.200 | ELGO communication | Alert | Communication time out | CAN communication between ELGO device and TOC box has failed (time limit exceeded) | 1) Check wiring between TOC box and ELGO device (Can signals) | |
Fault 60 : Self test ELGO failed | 60.254 | ELGO Autotest | Alert | Self test ELGO failed | Self test ELGO Error Level 4 | Noise on eSGC signal cable. Put a relay on the TOC box to open the load line when eSGC output is not active | |
Fault 60 : Magnetic Band missing | 60.255 | Magnetic Band ELGO | Alert | Magnetic Band missing | The ELGO device did not detect the magnetic strip | 1) Check the presence of the magnetic band 2) Check mounting of the magnetic band 3) Check mounting direction |